在庫管理術
在庫管理の見える化【在庫は可視化できる!脱エクセル・アナログの成功事例をご紹介】
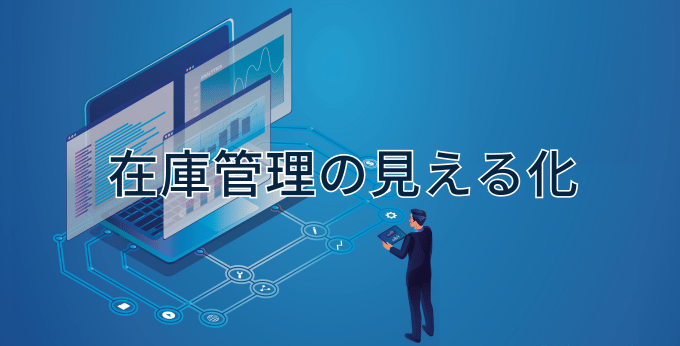
「どこに、何が、いくつ」保管されているかという在庫の管理情報を誰にでも分かる状態に保つことを在庫管理の見える化といいます。
この記事では自社の在庫管理を見える化する方法や、見える化を進めていく上での注意点について解説。また倉庫や工場の在庫管理の見える化に成功した事例も紹介します。
在庫管理は見える化できる?
在庫の膨大な点数やそれぞれのロケーションを前にすると、在庫管理の見える化をどのように進めてよいか迷うことが多いのではないでしょうか。
従来は棚札や棚カードの作成や、在庫ノートやホワイトボードへの記入、エクセルの手入力など、大半を人的労力に頼ったアナログな手法で在庫管理の見える化を図っていました。
さまざまなデジタルツールやIoT機器とクラウド型SaaSシステムを連携させることで、より効率的に在庫管理の見える化を実現できます。
在庫管理を見えるするメリット
在庫適正化に繋がる
過剰在庫の主な原因は
- リアルタイムの在庫量
- 在庫の消費スピード
を把握できていないこと、欠品への不安から過剰発注が常態化していることにあります。
在庫の見える化によって現在の在庫数や消費スピードといった在庫状況が把握できると、発注量や発注タイミングの見直し、在庫処分といった在庫適正化につながるアクションが取りやすくなります。
属人化が解消される
在庫管理は、発注タイミング、消費スピードや納品リードタイムの知識がある人に業務が集中する傾向があります。業務が属人化すると担当者不在の時に、「在庫の場所がわからない」、「在庫が少なくなっているが発注済みかどうかわからない」などの混乱が起き、発注遅れや二重発注のミスが発生しやすくなります。
在庫の見える化によって、在庫情報の共有がうまくいくと、複数人からなるチームによって円滑に業務がすすみ、属人化が解消、在庫管理担当者の作業負担・心理的負担も軽減されます。
作業効率化が進む
在庫の見える化によって過剰在庫解消が進むと、日々の棚卸をはじめとする作業工数を削減することができます。また在庫情報がオープンになることで、在庫確認を目的とするコミュニケーションコストも抑えることが可能です。
カイゼンを促進する
在庫の見える化をすすめると、今まで気がつかなかった在庫管理上のボトルネックが明らかになり、現状を踏まえた改善策を計画・実行することができるようになります。
消費期限切れで廃棄ロスが発生している在庫、発注回数が多く発注量を今より増やした方が良い在庫の存在が可視化され、業務カイゼンの糸口が見つかります。データにもとづき改善策実行後の効果測定も可能で、カイゼンのPDCAをうまく回すことができるようになります。
在庫管理の見える化の手法
5Sの定着
在庫管理では5Sというルールを決めることで、物理的に在庫の場所、量、状態が見えてきます。具体的には倉庫や在庫置き場の整理・整頓・清掃・清潔をすすめ、社内のしつけを徹底的に行います。
在庫管理システムの活用
在庫情報の見える化には在庫管理システムの活用が有効です。在庫管理システムは、IoT機器やバーコード、RFIDといったモノを認識するツールを使って、在庫データを効率良く収集し、蓄積します。またダッシュボードや在庫分析機能の活用で、自分では分析しにくい在庫状況を可視化することができます。
携帯端末から使いやすい「アプリ」を利用
在庫管理システムがクラウド型SaaSシステムである場合、インターネット環境さえ整っていれば、いつでも・どこでもシステムにアクセスして在庫情報を更新することが可能です。
そういったケースではシステムの機能のひとつに「アプリ」が搭載され、スマートフォンやタブレットなどの携帯端末でも使いやすい仕様になっています。端末のカメラ機能は「モノ」の認識に活用可能です。
そのため現場の作業者が「アプリ」を使って、日々目まぐるしく変わる入出庫状況をリアルタイムで情報更新したり、納品・納入の期日が迫っているモノの入出荷情報を更新したりすることで、遠隔での在庫管理や在庫状況の可視化に役立ちます。
在庫管理の見える化におけるハードルや問題点
①見えにくい在庫がある
遠隔の倉庫、鍵のかかった部屋、冷蔵庫等の密閉された空間は物理的に目が届きにくく、在庫補充対応が遅れることがあります。
また製造業を例にあげると、仕掛品、共通部品、副資材、設備のメンテナンス用の部品などは消費予測や全体数量が見えにくいモノです。また製品の性質上、選択嵌合部品をはじめ消費スピードが読めないモノ、施錠された状態での保管が必要な毒劇物も可視化が難しい在庫に当てはまります。
さらに倉庫だけでなく、現場付近の一時仮置き場や配膳棚に点在する在庫を可視化する難しさは製造業に限りません。各フロアの保管庫や備品庫に点在する在庫管理の見える化には多くの企業が頭を悩ませています。
②在庫データ集めに現場が疲弊する
デジタルツールを使って、必要な在庫情報を集めやすくなった一方で、バーコードやタグの読み取りやシステム入力など、在庫データ集めに関する作業が新たに発生し、そのことが現場の大きな負担となっています。
③データ収集からカイゼンに繋げられない
在庫データは集計・分析を経て、カイゼンのアクションに繋げたときに初めて価値を生み出します。しかしデータ活用ができる人材の育成には時間がかかるため、多くの企業がデータ活用人材の不足に悩んでいます。データの蓄積でストップしてしまい、カイゼンにつなげられないケースが多発しています。
在庫の見える化の課題を解消する鍵となるのが、在庫管理IoTソリューションです。見えにくい在庫を可視化し、在庫データ集めから分析まで自動化できるスマートマットクラウドをご紹介します。
在庫管理を見える化。倉庫や保管庫、工場の在庫を可視化する「スマートマットクラウド」
リアルタイムの在庫を見える化
スマートマットクラウドは、重さで在庫を数えるIoTの在庫管理サービスです。人の代わりに24時間365日在庫を監視し、データを蓄積。今まで見たいのに見えなかった在庫を見える化します。
重量IoT「スマートマット」の上に管理したいモノを載せるだけで設置が完了。スマートマットが重さから自動で在庫を検知します。
リアルタイムの在庫がPCやタブレットで確認できるため、遠隔管理可能で、倉庫、顧客先在庫、キャビネットや冷蔵倉庫等、目の届きにくい場所にある在庫管理に最適です。
ドラム缶や一斗缶の中の液体、粉物、ケーブル、大量の小さな部品など、目視では数えにくい在庫も可視化。点在する副資材や設備のメンテナンスパーツなど消費スピードが一定でない在庫も、発注タイミングを逃さず通知します。
最適なカイゼンアクションを見える化
スマートマットクラウドはAI×IoTで日次・週次・月次3つのレポートで分析結果に基づいた在庫最適化アクションを見える化します。
手動の棚卸ナシ、膨大なデータの分析の負担なしで、欠品リスクの警告、発注点の見直し提案、削減余地のある在庫特定など在庫最適化をもたらす具体的なアクションを受け取れます。
在庫消費量を見える化
スマートマット管理画面は、在庫の推移をグラフで見える化します。アナログな管理では見たくても見ることができなかったリアルタイム実在庫数、在庫の消費スピードのデータを可視化します。
しきい値を下回った場合、在庫状況を青・黄色・赤の3色でわかりやすく表示
不動在庫を見える化
スマートマットクラウドは優先的に在庫削減すべき不動在庫を特定します。在庫ごとに出庫されていない期間を特定し、金額ベースでグラフによって見える化します。
在庫データはクラウドに自動で蓄積されるので、面倒なタグやコードの読み取りは不要。
分析もデータをもとにソフトウェアが自動で集計するので、特別なスキル不要でご利用いただけます。
カイゼンにつながるアクションにクイックに移行でき、効果測定も簡単です。
在庫の置き場所を見える化
スマートマットクラウドは、1枚のマットにつき1アイテムを管理。アイテムごとに在庫置き場所が自然と定まります。スマートマットクラウドの導入が、在庫管理の礎となる社内の5Sの意識定着を強力にアシストします。
在庫見える化ツールを比較
(○=強 / △=標準 / ×=弱)
在庫管理の見える化の成功事例
▼高砂熱学工業株式会社様のインタビュー動画はこちら
▼在庫の見える化で過酷な倉庫作業を大幅減 東京ガスネットワーク株式会社
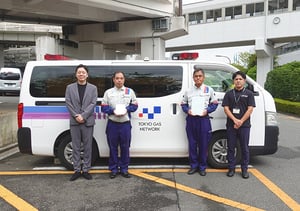
導入前は約800種類にも及ぶ工材を目視で確認していました。膨大な労力に加え、数え間違いが発生。夏は暑く冬は寒い倉庫での長時間作業が問題になっていました。導入後は、管理する工材をスマートマットに載せるだけ。あとはクラウドで管理、管理画面を開けばいつでも確認できるようになりました。
▼消費予測が困難な部品在庫を見える化 株式会社SUBARU
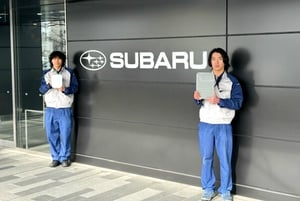
車の生産に必要な消費スピード予測が困難なバランスウェイトという部品があり、計画と実際の使用数にブレが生じていました。導入以前は緊急手配をなくすため、毎日社員が1.5hの工数をかけて数を確認し、発注をしていました。
重量で検知するという仕組みと簡易性が導入の決め手になりました。スマートマット単体で管理が完結できるという導入のしやすさに加え、他社でも使われているという実績があったため、社内での検討はスムーズに短期間で進みました。
▼毒劇物在庫の見える化で労災リスクを除去 三菱ケミカル株式会社
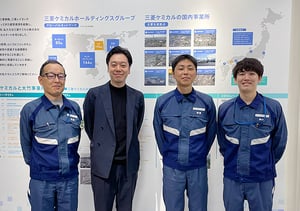
毒劇物保管庫の棚に並ぶ化学品約350品の管理では、使用前後の重量を量り、管理簿に記録、紙の帳票に書き起こし管理職の承認を取得、さらに月に一度は半日かけ棚卸を実施していました。棚卸では化学品を棚から運んで計量するため、労災リスクを伴なっていました。スマートマットの活用で、化学品の使用量と在庫量を見える化。負担が多く危険を伴っていた在庫棚卸業務を自動化できました。