在庫管理術
QCサークル活動とは【歴史・基本要素・目的とメリット・進め方・デメリット・品質管理の事例】
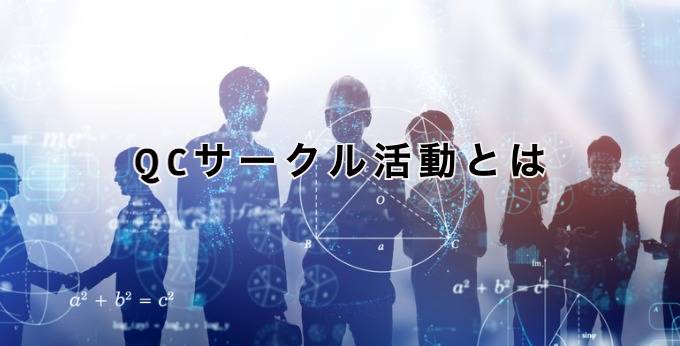
この記事では、世界に認められている日本のモノづくりの現場で品質向上の一端を担っているQCサークル活動について、歴史、基本要素や目的とメリット、進め方、製造業の事例についてわかりやすく解説していきます。
QCサークル活動とは
QCサークル活動について簡単にまとめると、現場で働く従業員・スタッフを小集団に分けて、品質管理・品質改善について自主的に話し合い、意見を出し合って、実際に行動に移していく活動のことです。
QCサークル活動のQC(英語:Quality Controlの略)は、「品質管理」を表します。
QCサークル活動は、主に製造現場の工場などで品質管理を目的に取り入れられており、小集団改善活動とも呼ばれています。

QCサークル活動の歴史
1950年、アメリカのW・エドワーズ・デミング氏により、日本の経営者に品質管理の考え方や統計的手法が伝えられました。これをきっかけに日本で独自に改良を加え、生まれたのがQCサークル活動です。
日本では、トヨタ自動車が「経営管理の画期的刷新」と「良質廉価な製品の生産と開発」を図るため、従来から行われてきた品質管理を強化し、1961年にTQC(Total Quality Control)を導入したことが有名です。
以降、トヨタ自動車では、QC活動も全職層で推進組織が整備され、スタッフが取り組む「QCチーム」(1963年)、現場の第一線の作業者が参加する「QCサークル」(1964年)など、全員参加のTQCが展開されていきました。
21世紀以降、会社を取り巻く環境は、グローバル化や急激な変化に対応するため、トヨタのQCサークル活動も、時代にあった活動に進化・拡大。
2004年から、G‐QCサークル活動(Grade up、Global、Toyota-Groupの3つのGを冠して命名)へと改められ、さらなる進化を遂げています。
QCサークル活動の基本理念と要素
3つの基本理念
1946年の創立以降、経営管理技術、「品質管理」を中心とする事業を推進している日科技連によると、QCサークル活動の基本理念は、以下の3つとされています。
- 人間の能力を発揮し、無限の可能性を引き出す。
- 人間性を尊重して、生きがいのある明るい職場をつくる。
- 企業の体質改善・発展に寄与する。
4つの基本要素
そして、この理念を実現するために欠かせないQCサークル活動の基本となる要素は以下の4つです。
- 人
- グループ力
- 改善力
- 管理者の支援
QCサークル活動の目的とメリット
QCサークル活動の目的は、品質管理と改善です。この目的を達成することにより以下のようなメリットが得られます。
- 顧客満足度アップ
- 不良品の減少による廃棄ロスや無駄を削減=コスト削減
- 稼働率や生産性がアップ
- 状況や現場が見える化できる
- 従業員・スタッフの自主性や解決能力が向上する
- 改善できたことによる達成感や満足がモチベーションを高める
- 優秀な人材育成につながる
QCサークル活動の手段と進め方
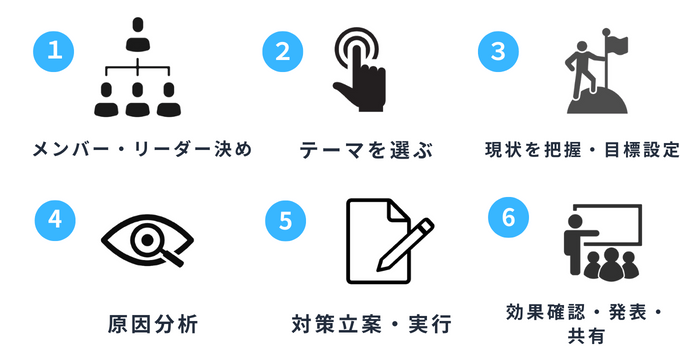
実際のQCサークル活動の手段と進め方を見ていきましょう。
STEP1 :サークルメンバーとリーダーを決める
一般的にQCサークル活動の小集団は10人程度とされています。これ以上多いと発言しないメンバーが出てしまうため、これを目安にメンバーを決めましょう。リーダー本人の意思やメンバーの意思を確認し、適任と思われるリーダーを選出します。
STEP2 :テーマを選ぶ
「何を改善するのか」、テーマを明確にしていきます。具体的には、不良品が頻繁に発生している、製造リードタイムに無駄があるといった実際に現場で起きている問題の洗い出しからスタートします。
何が品質を損ねているのかをコスト、緊急性などを考慮しながらピックアップし、現状、取り組むべきテーマを選びます。
STEP3 :現状を把握し、目標を設定する
不良品発生率、リードタイムの時間、作業フタッフが実際に働いている時間…などの具体的なデータを集め、問題点を把握します。
データをもとに、どれくらいの改善を図るのか具体的な数値目標(例えば不良品発生数を100から10に削減など)を設定します。
STEP4 :原因を分析する
問題が発生する理由を分析、検証します。この際に主に使われるのが特性要因図*や散布図*などです。
これらを使って、原因となる要因を明確にします。さらにグラフなどを加えて検証することで、より精密な原因の分析が行えます。
*特性要因図:ある問題に対してどのような要因が影響を及ぼしているかを洗い出して矢印で繋いだもの。できあがった図の形からフィッシュボーン(魚の骨)と呼ばれる。
*散布図:2つのデータの相関関係をグラフで示したもの。
STEP5 :対策を立案し、実行する
問題を改善し、目標を達成するための改善案を立案・実施します。
例えば、「製造に欠かせない資材の在庫不足が発生するため***円相当の機会損失が起きている」という問題の場合、「人力で行なっていたためミスが発生していた在庫管理と発注を自動化する」といった対策を立て、そのために必要なシステムや技術を導入する、というアクションを実施します。
STEP6 :効果を確認し、発表・共有する
効果測定を行い、どれくらい目標を達成できているのかを明らかにし、サークルメンバーに共有します。
すぐに改善することは難しいので、PDCAサイクルを繰り返して、少しづつ改善を進めていくことが重要です。
QCサークル活動のデメリット
実際に多くの製造業の現場で導入され、認められているQCサークル活動ですが、「時代遅れじゃないか」「廃止した方が良いのでは」という意見も見受けられます。その理由として以下のような点があげられています
- 惰性で行うようになってしまい、改善に至らない
- 業務に追われ、QCサークル活動の準備の時間が捻出できない
- なかなか効果が上がらず、モチベーションが保てない
- サークル活動が実際に役立っているという実感を持ちにくい
このようにQCサークル活動は、いきなり改善が見られるといった即効性の効果が得にくいため、モチベーションの維持が大きな課題となっているようです。
次の章では、人力による労力を削減し、具体的な数値で効果が確認できる今、話題のIoTについてご紹介していきます。
製造業の品質管理とIoT
新型コロナウイルス、人手不足などさまざまな問題に直面している製造業において、いかに効率化して正確に品質管理を行うことができるかが重要となります。
そこで注目され、近年続々と各企業で導入されているのが品質管理の自動化であり、その最も有効な方法として以下の2つが大きなキーワードとされています。
● DX(デジタルトランスフォーメーション)
企業の営みや産業全体をデジタルの力でよりよくしていく取り組み
● IoT(Internet of Things)
IoT=「モノのインターネット化」
IoT機器を導入することにより、「自動化」や「見える化」が可能になり、棚卸、現場作業の改善、在庫管理、工程管理、品質管理なども効率的に行えるようになります。
このように稼働状況や生産状況、在庫などのデータを分析することで、人力では発見しにくい問題や傾向なども把握できるようになり、生産性の向上やロスタイムの削減につながります。
デジタルテクノロジーを駆使して、企業経営や業務プロセスそのものを根本的に改善していくDX(デジタルトランスフォーメーション)を実現するためにIoTは欠かせない要素となります。
スマートマットクラウドがリアルタイムで工程を見える化
IoTで在庫管理を自動化、工程カイゼン・DX推進
スマートマットクラウドはリアルタイム実在庫の見える化で在庫管理、工程カイゼン・DXを進めるIoT SaaSプロダクトです。IoTで現場のモノの動きを捉え在庫管理を自動化、その上で工程内のモノの流れを分析し問題を見える化します。さらにリアルタイム実在庫データを武器に工程を跨ぐ流れの澱みを特定しDX、現場力の向上に寄与します。
在庫置き場に出向くことなくリアルタイムで管理画面から部品と仕掛品の在庫数を確認できます。在庫確認や補充タイミング把握のため、倉庫や工場内を走り回る必要はもうありません。
スマートマットクラウドは生産工程の進捗状況も可視化。
後工程からひとつ前の工程に、必要な部品を、必要なタイミングで、いくつ必要かを自動で伝えることで、製造業の生産プロセスに潜むさまざまな課題を解消します。
◆特徴
- 遠隔で在庫を一元管理:倉庫や各拠点の在庫を管理画面で一元管理
- 需要に見合った供給を実現:ひとつ前の工程に伝え、過不足なく生産できる
- 生産効率を最大化:リアルタイムかつ自動で伝え、ムダがない
製造業のスマートマットクラウド導入事例
スマートマットクラウドは、現在多くの製造業の現場で導入されています。
実際に導入された事例と効果をご紹介します。
この記事を書いた人
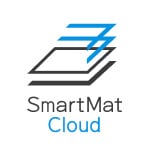
スマートマットクラウド メディア編集部
スマートマットクラウド メディア編集部です。業務効率化や業務の課題解決などをわかりやすく解説します!
【スマートマットクラウドとは?】
スマートマットの上にモノを置き続け、重さで数を数えるIoTサービスです。
ネジなどの部品、副資材・仕掛品・粉モノや液体の原材料まで、日々の在庫確認や棚卸・発注まで自動化します。