在庫管理術
不良率【PPMや歩留まりとの関係・計算式・許容範囲と目標値・原因と改善方法】
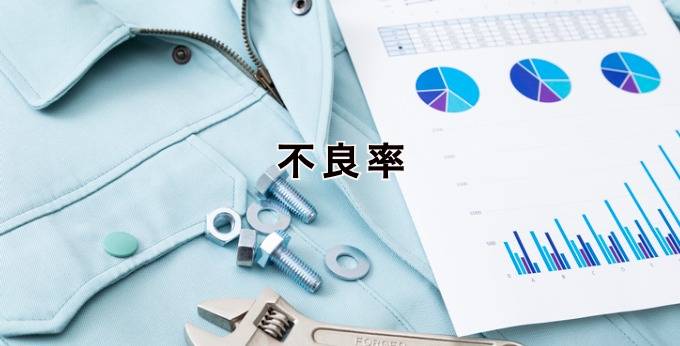
この記事では、製造業の品質管理や生産性向上のために欠かせない重要な指標「不良率」についてわかりやすく解説。PPMや歩留まりとの関係や計算式、許容範囲・目標値、不良品発生の原因と改善方法をご紹介していきます。
不良率とは
不良率(英語:Defect Rate)とは、製造業における製造工程で発生する不良品の割合を指します。
不良率が高くなれば…
- 売り上げや企業利益に悪影響
- 発見できずに販売されると顧客クレームが発生
- 良品を製造し直す労力やコスト増
そのため、不良率は品質管理や生産性向上を図る重要な指標とされています。
不良率と歩留まりの関係
製造業の不良率とあわせて知っておきたいのが歩留まりです。
製造現場における歩留まりとは、使用された原料や素材の量に対して生産された完成品の割合のことで、わかりやすく言うと、製造された製品のうち良品の割合を意味します。
- 不良率=不良品の割合
- 歩留まり=良品の割合
つまり、歩留まりが高ければ不良率が低くなり、歩留まりが低ければ不良率は高くなります。
不良率の計算式【PPMとパーセンテージ(%)】
不良率は、以下のパーセンテージ(%)を使った計算式で算出します。
不良率(%)=(不良品の数/総生産数)×100
具体例をあげると、3,000個の製品を製造している工場から30個の不良品が出た場合、(30/3,000)×100=1になるので不良率は1%となります。
そして、不良率はPPMという単位を使って数値化します。
PPMは、Parts Per Millionの略で、製造業における品質管理で使用されています。製品100万個あたりの不良品の数を示す単位です。
パーセンテージ(%)を使った計算式で算出した不良率をPPMで表す計算式は以下の通り。
PPM=不良率(%)×10,000
上記の具体例のように不良率が1%の場合、1%×10,000=10,000。PPMは10,000なので、製品100万個あたりの不良品は10,000個になります。
そして、不良率が低いほど、PPMも低くなります。
不良率の許容範囲・目標値
不良率の目標は、業種や製造する製品、生産規模などによって変わりますが、一般的に目安とされているのは標準偏差*である「σ:(シグマ)」が基準となっています。
そして、製造業において不良率の許容範囲・目標値は、「3σ(サン・シグマまたはスリー・シグマ)」または「6σ(シックス・シグマ)」となります。
具体的には、以下のような割合になります。
- 「3σ 」1000個の製品を製造した場合、不良品が3つ未満で発生する割合=99.7%
- 「6σ」 100万個の製品を製造した場合、不良品が3個発生する割合=99.9997%
製造業では一般的には3σを目指します。人命や安全性を第一に考えなければならない自動車業界などでは、より厳しく6σが目標値として設定されることが多いようです。
*標準偏差:統計学における散布度(バラツキ)を計測する手法。平均からのズレを表す数値でもある。
不良品が発生する主な原因
不良品発生の原因は、4M、5M、5M+1Eにあります。
- 「4M」Man(人)、Machine(機械)、Material(材料)、Method(方法)
- 「5M」4MにMeasurement(検査・測定)の要素を加えたもの
- 「5M+1E」5Mに環境要素を加えたもの
Man(人)ヒューマンエラー・人的ミス
4Mの基礎であるMan(人)とは、人=現場の作業員・スタッフのことです。
機械や材料、方法はすべて人の手によるものであることから最も重要とされています。
そして不良品の多くは、Man(人)ヒューマンエラー・人的ミスが原因です。製造過程においては、人による機械の制御や操縦ミス、材料の選別や分量の数え間違いや投入ミスなどがあげられます。
Machine(機械)ミス
製造業の生産の現場で稼働する機械や設備の故障、機械や設備のメンテナンス(掃除漏れなど)不足などが不良品の原因に。
Material(材料)ミス
製品を製造するには、さまざまな原材料や部品などの資材を調達することが必須ですが、材料の調達漏れや調達不足、材料の検査漏れが不良品の原因に。
Method(方法)ミス
製品を製造する方法が原因による不良品発生には以下のようなことがあげられます。
- 製造工程の標準化(決められた手順・方法)ができていない
- 製造する製品に沿ったマニュアルができていない
Measurement(検査・測定)ミス
原材料計測ミスや品質測定や検査ミスが不良品の原因に。
Environment(環境)ミス
製造業の工場内の温度や湿度、気圧管理ができていないことも不良品の原因に。
不良率を改善・下げる方法
不良率を改善するには、品質管理に欠かせない手法とされている4Mや5M、5M+1Eがしっかり守られているか?できているか?をチェックすることが重要です。
具体的には下記の項目をチェックします。
- ヒューマンエラー・人的ミスの防止
- 機械や設備の点検やメンテナンス
- 材料や資材の調達と検査の徹底
- 製造工程の標準化・マニュアルの確認
- 原材料計測・品質測定や検査の徹底
- 工場内の環境整備の徹底
しかし、現実問題として数多くのチェックを手動で行うのは困難です。そこでAIやIoTなど最新技術を導入し、どうしても人間の手では防ぎきれないミスを防止しようとする企業が増えています。
不良品発生の具体例
不良品発生の原因は、4M、5M、5M+1Eにありますが、実際に製造現場で起こっている具体的な例をご紹介します。
配合表(レシピ)やBOM(部品表)をもとに製品を製造します。人が行う作業工程では、どうしても以下のようなミスが発生してしまいます。
- 原材料の誤投入や投入漏れ
- 部品の付け忘れや付け漏れ
- 原材料の計量ミス
さらに、本来の正しい製品を製造し直す、手間やコスト負担もかかるため、不良品発生の原因を早期に発見することが重要です。
原材料の計測ミスや誤投入を防止するIoT在庫管理「スマートマットクラウド」
現場のあらゆるモノをIoTで見える化するDXソリューション「スマートマットクラウド」を使えば、在庫管理、棚卸の自動化が可能になります。
IoT重量計による重量計測のため、数えにくい液体・粉末形状の資材、多品種で類似品の多い機械消耗品、管理の難しい仕掛品も正確に計測。
倉庫や各拠点に点在している在庫、冷蔵庫や保管庫の中など、見えない場所の在庫もIoT重量計に載せるだけで遠隔から一元管理できます。
資材や原材料管理をIoT重量計で自動化することで、在庫重量の変動をリアルタイムに把握。数え間違いや誤投入、付け漏れや付け忘れなど不良率発生の原因を早期に発見します。
◆特徴
- 在庫管理工数削減:日次での在庫確認と発注を自動化。リモート管理もOK!
- 欠品・過剰在庫防止:自動発注機能の活用で適正在庫を維持
- 在庫差異を縮小:重量計測で正確な在庫数を自動記録
- 在庫管理の形式知:属人化しやすい在庫管理ノウハウを共有
この記事を監修した人
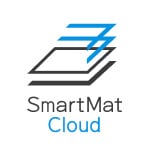
製造DX協会
製造DXに取り組む製造業・スタートアップ・エキスパートが集結し、企業の垣根を越えてノウハウを共有しながら社会全体に最適な製造DXガイドラインを発信しています。
https://manufacturingdx.org/