在庫管理術
歩留まり改善【歩留まりの計算方法や不良率との関係、低下箇所の発見方法とは?】
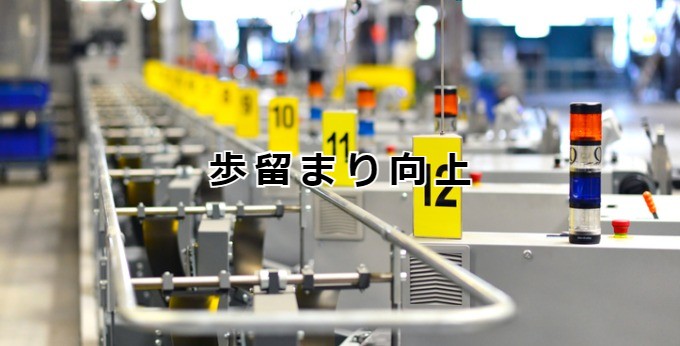
こちらは、製造業の方向けに「歩留まり」についての考え方や計算方法を掲載しています。歩留まりが低い要因の解明や改善に役立つシステムもご紹介。歩留まりの低さに課題を抱えている方は、ぜひご一読ください。
製造業における「歩留まり」とは?
歩留まりとは?わかりやすく解説
製造業における「歩留まり」とは、生産された製品のうち良品の割合のことです。
歩留まり率とほぼ同義で使われる用語で、英語では“率”や“割合”を示すRateを使って「Yield Rate」として表現されます。
現場目線で具体的に説明すると、原料の投入量から期待される生産量に対し、実際に市場に出せる良品として完成した製品数量との比率として扱われます。
歩留まりの優劣は「高い・低い」で表現し、歩留まりが高ければ良品率が高く、投入された原料・生産ライン・生産方法・生産技術が優れているという指標になります。
一方で歩留まりが低いということは、製品の不良率や原料廃棄ロスが多く、製造コストの圧迫に繋がります。歩留まりが低くなる要因はさまざまですが、健全な経営状況を図るためには歩留まりを向上させる必要があります。
製造業でも歩留まりの考え方・計算方法はひとつではない
製造業でも、歩留まりに関する考え方は大きく2通りに分けられます。
部品の組付/組立のようにBOMをベースに製品を製造する機械や装置メーカーは、原料となる部品の配膳セット100組に対し期待できる生産量は常に100個。そのため、歩留まり率は生産数量に対する良品数を把握するだけで算出できます。
一方、薬品や液体・粉体の配合/塗布のように配合表をベースに製品を製造する化学メーカーは、原料に対して期待できる生産量がそもそも100%ではない場合があります。生産技法や生産ラインによっては装置内に残留したり、生産中に飛沫することを前提として製造されるためです。
その場合の「投入原料に対して期待できる生産量の割合」は、例えば90%*1が正常的な値となります。さらに生産量のうち不良率*2が10%となった場合の歩留まり率は、
0.9-(0.9×0.1)×100%=81%となります。
*1:当該製品の原料廃棄量や完成品量の蓄積データから平均的な期待値を算出した値
*2:後述
つまり歩留まりを「原料に対して期待できる生産量」と「生産量のうち、良品と不良品」ふたつの考え方と計算方法の掛け合わせで歩留まり率を算出している2段階方式となります。
また可食部以外を廃棄する食品加工メーカーもどちらかというと、化学メーカーに近い歩留まり率の概念を持っています。
歩留まりを考える上で外せない「不良率」とは?
不良率とは生産工程のなかで発生する不良品の割合のこと。前述した歩留まりの考え方では必ずしも「歩留まり」の反対が「不良率」とはなりませんが、歩留まりが高ければ不良率が低い、歩留まりが低ければ不良率は高くなるのが一般的です。
また通常では、過去の生産履歴などから想定内の不良率の数値があり、それを基に生産効率の評価に利用されます。但し想定内の不良率を大きく逸脱すると、生産ラインの故障や原材料の品質異常、甚大なヒューマンエラーなど大きな異常やトラブルがあったと考えられます。
さらに生産ロットごとの不良率は、そのロットの品質評価の指標としても用いることが可能です。例えば、不良品が多ければ良品と認められる製品も規格の閾値ギリギリの品質のモノが多いと予測されるため、製品全体の品質基準が低いと見なされます。
逆に不良品が少なく、不良率が低ければ良品と認められる製品が十分に規格内にあると想定され、製品全体の品質基準が高いと考えることが可能です。このように、不良率は生産効率の評価はもちろん品質の評価に利用されることがあります。
歩留まり低下の要因と歩留まり向上のための改善点
歩留まり低下の要因
歩留まりの低下には以下のようにさまざまな要因があります。
- 原料に不良品がある
- 原料へのコンタミ*2混入
- 原料誤投入や機械条件設定誤りなど準備の人的ミス
- 生産時のコンタミ混入
- 生産時のヒューマンエラーによる不良品の発生
- 機械トラブル等の生産中断による不良品発生や原料ロス
- 機械の経年劣化による不良率の上昇傾向
- 精度の低い生産方法による不良率の向上
*2:コンタミとは、コンタミネーション(contamination)の略。不純物、もしくは不純物が混入すること。
歩留まり向上・改善のために必要なこと
歩留まりを改善するには、どの段階で歩留まり低下の要因が発生しているかをまず知ることが先決です。
始めに使用する原料に異常がないかを確認します。納入時に規格に沿って検品する製造業もあれば、化学工業や食品加工では生産ライン投入直前に検品が必要な場合もあります。
また製造工程に入った後は、原料の投入量と良品の仕上がり量の正確な把握が必要となります。複数工程がある場合は、投入した原料とそれぞれの中間品、完成品の数量を正しく把握することが不可欠。生産ラインの仕組みや技法によっては、廃棄量の都度把握も歩留まり算出のために必要です。
このような工程間のモノや数量の流れは、IoT重量計によりリアルタイムで重量変動を検知するシステムで的確に把握することが可能です。

歩留まり低下箇所を早期発見し、要因解析を可能にする方法とは
IoT重量計を活用することで、製造工程の原料投入から中間品・完成品・廃棄量のモノと数量の流れをリアルタイムで把握できます。生産管理部署で遠隔から一元管理すれば、原料・中間品・廃棄量のイレギュラーな数量変動の早期発見が可能です。
また蓄積されたデータを月次や週次で解析することで、歩留まりが低くなりがちな工程や時間帯を可視化。複数工程や24時間稼働の生産現場では、さまざまな情報に埋もれやすい歩留まりを、「重さを測定し、データを転送する」というシンプルなシステムで洗い出し、問題解決の重要なトリガーとなり得ます。
歩留まり低下のポイントをリアルタイムで特定できる「スマートマットクラウド 」
スマートマットクラウドはリアルタイム実在庫の見える化で在庫管理、工程カイゼン・DXを進めるIoT SaaSプロダクトです。IoT重量計で現場のモノの動きを捉え在庫管理を自動化、さらに工程内のモノの流れを分析し問題を見える化します。リアルタイム実在庫データを武器に工程を跨ぐ流れの澱みを特定しDX、現場力の向上に寄与します。
倉庫や現場の資材仮置き場にわざわざ出向くことなく、原料・中間品・廃棄品・完成品の重量推移をクラウド上でデータ管理できます。イレギュラーな重量変化を早期発見し、またデータの蓄積により歩留まりが低くなりがちな工程や時間帯を見える化。歩留まり低下ポイントの特定に貢献します。
さまざまな自動発注に対応
お客様の発注先に合わせた文面でメール・FAXの送信が可能です。
在庫圧縮を促進
推移を把握できるグラフで適切な在庫量を判断し、在庫圧縮を促進します。
置く場所を選びません
スマートマットはA3サイズ〜A6サイズまでの4サイズ展開。ケーブルレスで、冷蔵庫・冷凍庫利用も可能。
API・CSVでのシステム連携実績も多数
自社システムや他社システムと連携を行い、より在庫管理効率UPを実現します。
リアルタイム実在庫のデータを収集、分析、遠隔管理が可能
スマートマットクラウドはリアルタイム実在庫のデータを収集、分析、遠隔で管理。工場内の自動化、スマートファクトリー化をサポートするIoTソリューションです。
IoTで現場のモノの動きを捉え在庫管理を自動化、その上で工程内のモノの流れを分析し問題を見える化します。さらにリアルタイム実在庫データを武器に工程を跨ぐ流れの澱みを特定しDX、現場力の向上に寄与します。
在庫置場に出向くことなくリアルタイムで管理画面から部品と仕掛品の在庫数を確認できます。在庫確認や補充タイミング把握のため、倉庫や工場内を走り回る必要はもうありません。
スマートマットクラウドは生産工程の進捗状況も可視化。
後工程からひとつ前の工程に、必要な部品を、必要なタイミングで、いくつ必要かを自動で伝えることで、製造業の生産プロセスに潜むさまざまな課題を解消します。
AI x IoTで在庫最適化をし続けられる
スマートマットは、最新データ(入出庫の理論値ではなく、現場の実数データ)を溜め続けます。
そして、その大量データをAIが監視・解釈・検知。問題をタイムリーに抽出して改善を提案するので、常に在庫の最適化をし続けることができます。
◆特徴
- 遠隔で在庫を一元管理:倉庫や各拠点の在庫を管理画面で一元管理
- 需要に見合った供給を実現:工程ごとの進捗を瞬時に共有。過不足なく生産可能
- イレギュラーの早期発見:原料投入時の重量変動に問題があればエラーをお知らせ
- 生産効率を最大化:リアルタイムかつ自動で伝え、ムダがない