在庫管理術
生産リードタイム【製品価値を下げない効果的な短縮方法とは?】
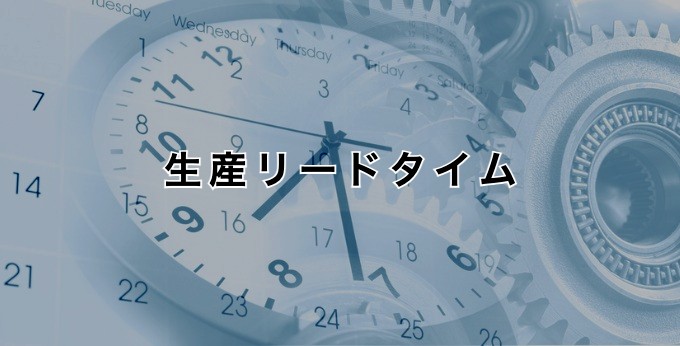
生産リードタイムとは?
生産リードタイムとは、原材料の出庫・搬入を含む外段取りから、生産工程・検査工程を経て、梱包され製品として出荷されるまでにかかる時間・日数の合計のこと。英語では「production lead time」と表し、また製造リードタイムと呼ばれることもあります。
似た言葉にリードタイム、もしくはトータルリードタイムがありますが、これは顧客が商品を発注してから納品が完了するまでのトータルの時間・日数の合計です。
トータルリードタイムは生産リードタイムに原材料の調達にかかる調達リードタイムや商品の発送にかかる日数を加え、また納品先で検品がある場合はこの日数*1も含みます。
各種のリードタイムは、業種、業態、製品などによってやや考え方が異なります。ただし、重要なのは各リードタイムを最適化して、滞りなく製品を顧客の元に届けることです。
*1:配送リードタイムとも言う
生産リードタイムと納期
納期は商品を納品する期限のことで、生産リードタイムのように「何日間」と日数を用いて表すものとは異なり、「◯年◯月◯日」と具体的な日時で表します。
しかし納期と生産リードタイムは密接な関係があります。納期までの日数が短すぎて生産リードタイムが超過する場合は納期に間に合わず、反対に日数が長すぎる場合は仕上がった製品による在庫の圧迫・集金や請求業務の遅れに繋がります。
また受注サイクルがある程度決まっている製品や大量生産している製品について、納期が問題になることはほとんどありません。
しかし多品種小ロットを扱っている・単発での受注がある場合は、生産リードタイムだけでなく原料の調達リードタイムなども配慮し、営業も交えて納期調整を行ったほうがよいでしょう。
生産リードタイムの計算
生産リードタイムは生産開始日を求める計算方法に利用します。生産開始日の求め方は製品オーダーのロット数が固定されている場合と、ロット数が変動する場合の2通りあります。
●固定されている場合 ●変動する場合 |
*2:保全日数とは安全リードタイムとも言い換えられ、各種リードタイムに対してその変動する誤差と作業員の安全も考慮し、安全分として設定するリードタイムのこと。一般的には生産リードタイムに付加される
*3:下線部がロット全数の生産リードタイムとなる
生産リードタイム◯日と言われたら?
例えば、生産リードタイムが3日間と言われた場合、工場の稼働状況も把握して実際にはいつ製品が仕上がるのか確かめなくてはいけません。
同じ24時間稼働の工場でも3班3交代なら通常、土日はお休み。4班3交代なら工場は土日も稼働している場合があります。
また、2班交代の15〜16時間体制か一般的な8時間体制かによっても、同じリードタイム3日間でも加工に費やす時間は全く違います。加工に費やす時間が変われば、製品価格も変わってきます。
さらに製品の加工内容によっては工程途中でのライン停止が不可能な製品もあるので、いつ生産を開始すべきかは、生産リードタイムだけではなく工場の稼働日も考慮して決めるのがマストです。
生産リードタイムを短縮するには
製品を加工する上で、生産ラインの加工スピードを速くすることが最も手取り早い生産リードタイムの短縮に繋がると思われがちですが、実際にはそうではありません。
ベルトコンベア方式で人や機械が流れてきた製品を組み立ていく場合は、現行の速度以上にするのは物理的に無理な可能性があります。
その他の生産方式でも生産速度をひとつ変更するには、製品開発の段階から製品仕様を見直し、作業標準書を変更する必要があるなど4M変動のひとつとなります。
そのため、加工スピードを上げることは有効な短縮方法ではありません。何よりも生産工程や検査工程を大きく変えることは、製品の価値を下げる可能性を孕んでいます。
それではどのようにすれば、製品の価値を下げることなく生産リードタイムが短縮できるのか、詳しく解説していきましょう。
在庫管理の適正化・DX化で生産リードタイムを短縮
原材料の出庫・搬入の外段取りや、生産ラインや品質検査装置の条件設定や微調整などの内段取りにかかる時間を短縮することは、生産リードタイムの短縮に繋がります。
特に外段取りにおける原材料の出庫・搬入は以下のように、さまざまなムダが隠れている可能性があります。
①:原材料がどこにあるか分からず、探す必要がある②:手書きの出庫伝票を資材係まで持っていく必要がある
③:搬入にフォークリフトを使う必要があるが、操縦者が不在
④:原材料の一時仮置き場がない、中央倉庫まで遠い
①は5Sの中の整理・整頓ができていないことで発生する7つのムダのうちの「動作のムダ」です。在庫を整理・整頓し、どこに何があるかひと目でわかる工夫をすることで動作のムダを解消できます。
また②もかなりアナログな「動作のムダ」であり、これにかかる時間を短縮すれば生産リードタイムの短縮に繋がります。
②の解消には、コードやRFIDもしくは重量センサを導入してモノの在庫管理をDX化し、入出庫の際はアプリやスキャナーで読み取る、また入出庫の在庫情報はクラウドに転送されPCで一元管理できる、といった在庫管理の自動化がおすすめです。
さらに③、④は現場の「手待ちのムダ」や「運搬のムダ」に直結しており、生産管理部隊が生産計画や現場周りの導線を根本的に見直す必要があります。
生産計画を短いサイクルで見直すことで、生産ラインの滞留や乱れによる原材料の搬入待ちを軽減することが可能です。また現場近くに資材の一時仮置き場を造ることで、外段取りがスムーズに進み、生産リードタイムの短縮に繋がります。
複数工程なら工程間の連携を取り生産リードタイムを短縮
複数工程なら工程間の滞留時間も生産リードタイムに含まれます。この滞留時間が長くなればなるほど、生産リードタイムも長くなります。
滞留時間が長くなる要因には、生産工程での「澱み」つまり不良品が発生することでの手直しや、部品や仕掛品の欠品による生産ラインの停止といったトラブルが含まれます。
また前工程は完了しているのに、モノや情報の流れが上手くいっておらず後工程が停滞することもあります。
こういった淀みや情報・モノの流れを整備する「整流化」や、後工程のモノの使用をトリガーとし、前工程の欠品をなるべく少なくする「かんばん方式」を活用することで工程間の滞留時間を短くすることが可能です*4。
また生産計画にムリ・ムダがないことはもちろんですが、現場レベルで工程間の連携が取れているかどうかも検証しましょう。自工程だけでなく相互の進捗度合いやモノの仕上がり量などをモニターでひと目で判断できる工夫が必要です。
さらに何らかのトラブルがあった際には生産管理部隊だけでなく、現場の各班も相互に協力し合える、といった作業員全体の習熟度や問題解決力を高める教育・訓練制度を設ける必要もあります。
こういったことの積み重ねが、複数工程における滞留時間を減らし、全工程にわたる生産リードタイムの短縮に繋がります。
*4:整流化・かんばん方式のいずれもトヨタ生産方式におけるJIT(必要なモノを必要なときに必要な量だけ生産し、ムダを徹底的に排除する効率的な生産方式)の基本理念を支える手段
生産リードタイム短縮に直結する「スマートマットクラウド」
スマートマットクラウドはリアルタイム実在庫の見える化で在庫管理、工程カイゼン・DXを進めるIoT SaaSプロダクトです。IoTで現場のモノの動きを捉え在庫管理を自動化、その上で工程内のモノの流れを分析し問題を見える化します。
さらにリアルタイム実在庫データを武器に工程をまたぐ流れの澱みを特定し、現場力の向上に寄与します。
中央倉庫や一時仮置き場にわざわざ出向くことなく、リアルタイムで管理画面から資材と仕掛品の在庫数や在庫場所を確認できます。在庫確認や搬入・前工程の進捗待ちのため、倉庫や工場内を走り回る必要はもうありません。
在庫管理や資材の入出庫をスムーズにするシステム・アプリ
スマートマットクラウドのアプリを使えば、入出庫伝票の作成や使用状況のPCへの入力も不要。スマホアプリでカンタンに読み込み・クラウドにデータを転送し、PCで一元管理できます。
現場の作業員も在庫管理係も、入出庫の手続きに要する時間が削減されることで生産の段取りがスムーズとなり、生産リードタイムの縮小に繋がります。
別工程のモノの量を可視化できる重量センサ
複数の資材や仕掛品を扱う複数工程において、従来のかんばん方式では別工程のモノの仕上がり量が見えにくく、そのことが前工程の滞留在庫や後工程の欠品といった、工程間の澱みの原因となっていました。
スマートマットクラウドは、各工程ごとの原材料・仕掛品を重量センサで自動計測し数量をリアルタイムで可視化。
生産管理システムへの入力の手間や、コミュニケーションコストをかけることなく、工程間の連携をスムーズにし、生産リードタイムを短縮します。
◆特徴
- 過剰在庫の解消:後工程の状況把握で、欠品を回避できる最小個数での補充を実現
- 生産リードタイムの短縮:欠品によるライン停止や生産遅延のリスクを軽減
- コミュニケーションコストの解消:在庫の一元管理で時間を要する部署連携が不要に