在庫管理術
製造業DXが進まない理由と対策【推進のポイントと事例を解説】
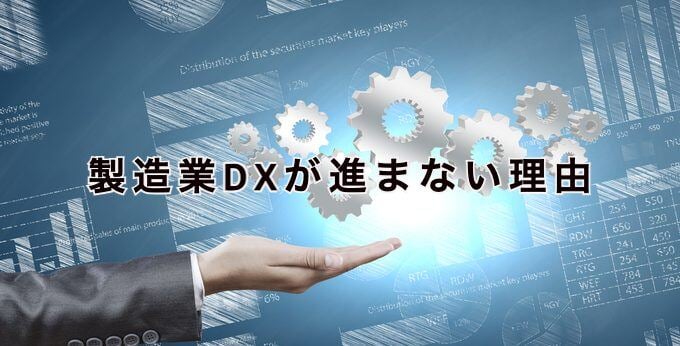
製造業企業がDXに着手したもののなかなか進まない理由はどこにあるのでしょうか。人材の不足、コスト負担、現場の抵抗、要因はいくつも思いつきますが、日本の製造業の特徴そのものにも原因があります。
この記事では日本製造業DXが遅延しやすい理由を明確にし、企業がDXを推進し成功させる方法やポイントを解説します。
製造業DXが進まない背景
すり合わせを得意とする日本の製造業
日本の製造業でDXが遅れている理由に、日本のものづくりは「すり合わせ」を必要とする製造を得意としていることが挙げられます。すり合わせとは、製品を構成している部品や材料を組み合わせる工程で調整を行い、最適化することをいいます。
すり合わせが必要な代表的な製品は自動車で、自動車製造は日本の基幹産業となっています。乗り心地や運転のしやすさを追求する国産自動車の性能・品質は、国際的に高い評価を受けています。
デジタルによる置き換えが困難なすり合わせ
一方で部品を製造工程で微調整を繰り返しながら組み合わせるため、「すり合わせ」を実施する製造では、現場作業員に高い技術力や経験が求められます。DX推進の観点から見ると現在手動で行っている作業をデジタルで置き換えにくいことを意味しています。
工程間やサプライヤー同士のすりあわせ
日本の製造業ですり合わせが行われるのは部品と部品の組み立て時だけではありません。日本が得意とするものづくりは、機能と部品が1対1で対応するというより、機能と部品の対応構造が複雑な関係になっています。製品の設計情報の繋ぎ方を製品アーキテクチャといい、構造が複雑な製品はインテグラル型に分類されます。
インテグラル型の製品の製造には、工程と工程の間、使用する部品を製造するサプライヤーとの間で綿密に連携を取り調整し合うことが求められます。部分的にDXソリューションを導入しても、他の工程や、関連企業との調整が多く入るため、DX化の効果を実感しにくいと考えられてきました。
製造DX×日本的製造業のポイント
カン・コツの見える化
日本製造業の特徴を踏まえ、DXをどのように活用したらいいのでしょうか。有効なのは、技能継承が難しい職人技、いわゆるカン・コツをデジタル技術で見える化する方法です。
言語化が難しく、いままでマニュアルに落とし込めなかった職人技を動画を撮る、IoTセンサーでデータを収集することで職人の技術を形式知に置き換え、製造プロセスに落とし込むことで平準化を進めます。
既存設備に組み合わせるソリューションを選択
現場の技術力が高い日本の製造業では、大規模な設備投資よりも、自分たちで技術力を高めることを優先する文化が根付いています。DX推進に着手する場合は大規模な業務フローを伴わない、既存の設備に組み合わせ可能なソリューション導入から始める方法があります。
他工程・関係企業の在庫を可視化
これまで密に連絡を取ることやシステムへの頻繁な手入力で把握していた他工程や関連企業の実在庫量の変動をIoTセンサーを使ってリアルタイムに把握することで作業計画や受注予測が立てやすくなります。
製造業DXは「スマートマットクラウド」で
日本製造業は「すり合わせ」という難易度の高く流出しにくい技術のおかげで、製品は高い品質を誇り、国際競争で優位性を保っていました。
「スマートマットクラウド」はモノの重さを「スマートマット」で計測し実在庫の数を可視化します。これまでDX化が難しかった日本製造業のすりあわせの技術をデジタルでサポートし、職人技の安定した継承を実現します。
不良やミスの予兆検知・予防
BOMと異なる動作を事前に察知し、部品の数え間違いや添加剤の投入ミスといったヒューマンエラーを防止します。
客観的なデータが不足し、後継への引き継ぎのハードルが高かった作業の属人化を記録や教育のコストをかけることなく解消します。
既存設備やシステムの入れ替え不要
スマートマットクラウドの導入に大掛かりな工事やシステムの入れ替えは発生しません。
スマートマットの上に管理したいモノを載せるだけで設置が完了。あとはマットが自動でモノの在庫を検知、クラウド上でデータを管理します。
サプライヤー間の在庫を見える化
物理的に離れた自社のユニット工場間や、上流サプライヤーから下流工場までの在庫状況を可視化します。これにより、発注側は在庫の消費量をリアルタイムで把握でき、調達リードタイムの短縮が可能になります。
製造業DX推進の成功事例
この記事を監修した人
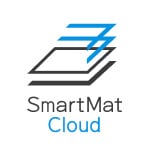
製造DX協会
製造DXに取り組む製造業・スタートアップ・エキスパートが集結し、企業の垣根を越えてノウハウを共有しながら社会全体に最適な製造DXガイドラインを発信しています。
https://manufacturingdx.org/