在庫管理術
製造DXソリューション
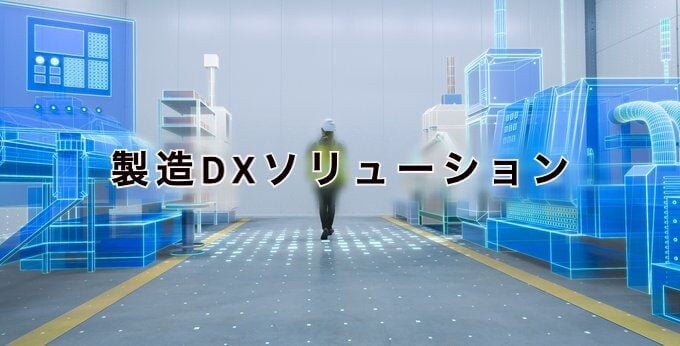
製造DXソリューションをどう進める
製造DXソリューションとは?
製造業が直面している課題をデジタルで解決すること、またはデジタルタービスのことを製造DXソリューションといいます。
海外と比較すると日本製造業DXはどうしても遅れが目立ち、いまだにベストプラクティスが見つかっていない状況に置かれています。
その背景には技術力が高い日本の製造業の特徴がありました。この記事では日本の製造業業が、既存の業務をデジタルにおきかえるデジタライゼーションにとどまらず、デジタルで課題を解決していくのに役立つポイントをお伝えします。
DXへの「取り組みにくさ」に直面する国内製造業
DXに対する「取り組みにくさ」の理由
国内の製造業が、DX推進に取り組みにくさを感じるのはなぜでしょうか。その背景に国内製造業の2つの特徴があります。
- 強い現場力
- 個別機械を組み合わせたライン設計
自律的に考えて改善を繰り返す強い現場力
まず、日本の製造業は工程内で自律的に考え、カイゼンをくり返しながら品質を作り込んでいく、強い現場力を持っていることが理由として挙げられます。
日本の製品の品質を支える強い現場力は、決められたひとつのルールに従い、効率作業に徹する欧米式製造DXソリューションとは相性が良くなく、そのことが製造業DX推進の遅れにつながっています。
個別機械を組み合わせたライン設計
もうひとつの理由として、国内の多くの企業が工程ごとに個別に機械を組み合わせ、自社で最適なライン設計をしていることが挙げられます。
製造ラインの構想・設計を実施する企業、ラインビルダーの活用がさかんな欧米式製造DXソリューションと比較すると、生産技術を磨きやすく、製品の品質を高めやすいメリットがありますが、効率化の追求や技術の継承がしにくいという性質も持ち合わせています。
現場力を活かす「日本式製造DX」とは
レトロフィット×横連携
日本のものづくりの強みである現場力を活かすには、各領域のデジタルソリューションを現場にレトロフィットさせる方法が適しています。
レトロフィットとは、既存の機械に新たな機能を追加して機械の性能を向上させることを言います。製造DX協会が提唱する日本式製造DXは、“人”を中心とする考え方を大切にします。既存のノウハウは活かし、デジタルを新たな武器として継続改善を可能にします。クラウドと柔軟なデータ連携があれば、全体最適化も実現可能です。
部分的展開からのクイックウィン
変化に対し最初は慎重な姿勢が強くあらわれやすいのも日本のものづくりの特徴です。
工場で製造DXソリューション導入に対し反発がある場合は、手始めにまず一部領域でDXを展開し、自社事例をクイックウィンに作ることが肝要です。そこから草の根的にDX推進が広がりを見せ、最終的にはDX推進に反対していた層も動かすことが可能です。
外部のDX伴走者をミカタに
製造DXソリューション導入・活用には製造現場の知見と、デジタル領域の知見が必須となります。デジタル人材が充分に確保できていない場合は、デジタルに精通している外部の伴走者を見つけアドバイスを得ながら、社内で現場サイエンティストの育成を進めていく必要があります。
在庫管理・工程管理DX「スマートマットクラウド」の導入にあたっては、導入支援からテクニカルサポートまで、各専門スタッフが対応いたします。
DX推進の足がかりに!スマートマットクラウド
当社の在庫管理・工程改善システム「スマートマットクラウド」は在庫の重さを「スマートマット」で計測、これまで見たくても見ることができなかった実在庫の数をデジタルに可視化します。
スマートマットの上に管理したいモノを載せるだけで設置が完了。あとはマットに搭載されたIoTが自動でモノの在庫を検知、自動でデータを取得します。
工程内でのモノの動きのデータを自動で取得しクラウド上に保存。製造DX推進をスマートマットクラウドが後押しします。
手入力“ゼロ”で、リアルタイムに実在庫を把握
導入は現場への負担もかからず、スモールスタートが可能。直感的にわかりやすい仕組みで社内の現場サイエンティスト育成にも最適です。DX推進のクイックウィン事例の創出で現場力をさらに高め、製造DXを成功へ導きます。
不良やミスの予兆検知・予防
BOMと異なる行動を事前に検知。組み付け部品の数え間違い、添加剤の投入ミスなどのヒューマンエラーを防ぎます。蓄積されたデータの分析により設備状況の変化やトラブル発生の仕組みを突き止め、問題発生を未然に防ぎます。
戦略在庫の適正化
一般的なカンバンと違い、部品の需給がリアルタイムで見える化。需給の過不足が解消され、戦略在庫が最適化されます。もちろん、カンバン管理体制下へのサポート導入も可能です。
生産リードタイムの短縮
一部でなく、工程すべてのモノの流れが可視化されるので、ボトルネックの洗い出しが容易に。工程全体を俯瞰したカイゼンが可能となり、生産リードタイムが短縮されます
製造業DXの製品を比較、検討するサイト「JET-Global」で製造業向け在庫管理システムとして紹介されました!
『製造業DXのおすすめメーカー・製品を比較するメディア JET-Global』の以下ページにて、弊社のスマートマットクラウドが紹介されました!
<スマートマットクラウド掲載記事>
「製造業向けの在庫管理システムとは?
こちらもぜひご一読ください。