在庫管理術
TOC理論|基本の考え方を製造業のボトルネック工程を用いて解説
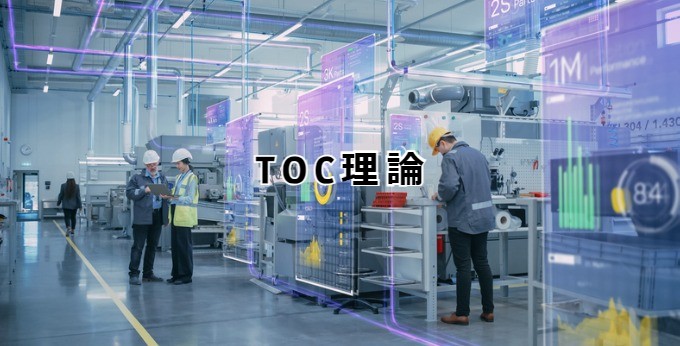
この記事では、製造業におけるTOC理論について紹介します。TOC理論の要となる5段階集中プロセスを具体例を交え説明し、さらに「もはや古い」と言われる原因となったデメリットやトヨタ生産方式との違いについても解説。TOC理論のマネジメント確立に役立つIoTソリューションについても紹介しているので、ぜひご一読ください。
TOC理論(制約条件)とは?
制約条件の理論をわかりやすく解説
TOC理論とは、イスラエルの物理学者エリヤフ・ゴールドラット氏が「The Goal*1」という書籍で提唱したマネジメント手法のこと。英語では「Theory of Constraints」と言い、直訳すると「制約条件の理論」となります。
あらゆる業界の関連業務や一連工数で、ある業務・工数において著しくスループット*2が低い、つまり何かしらの制約がかかっている場合、これを解消するマネジメント手法として用いられています。
全体のパフォーマンスを底上げするマネジメントとは違い、制約条件に集中し改善・カイゼンを行うので、最小限のコストと時間で効果が出るメリットがあります。
製造業の場合では、ボトルネック工程のように著しくパフォーマンスが低下している工程を改善するためにTOC理論を用います。当該工程の生産条件や人員、オペレーション内容に集中して改善策を打ち出すことによって、最大限の効果を引き出します。
*1:イスラエルの物理学者、エリヤフ・ゴールドラットによる著書。「The Goal」はビジネス小説の形態を採っており、その中でさまざまなマネジメント理論が提唱されている(Wikiより)。またゴールドラットは製造業の複数工程における「ボトルネック」について考察し、そこからさまざまな業種にも通じる「TOC理論」を展開した。
*2:スループットとは処理能力や処理スピードのこと。製造業では生産出来高/生産量で表す場合が多い。また、製品の売上高から製造・販売に掛るコストを差し引いた売上金額を「会計スループット」とし、生産能力を測るケースもある。
「5段階集中プロセス」とは?
TOC理論を用いて制約条件を打破
TOC理論で提唱されている「5段階集中プロセス」とは、制約条件の理論に基づいたマネジメント手法のこと。ここでは製造業における複数工程でボトルネック工程があった場合、ボトルネックを制約解消するプロセスを解説。また各Stepごとに具体的な改善例も併せて紹介します。
Step① ボトルネック工程にある制約条件を見つける
ボトルネック工程を特定するだけでなく、スループット低下要因となっている制約条件をまず見つけましょう。制約条件としては、次のようなケースが挙げられます。
- スタッフのスキルが低く、時間が掛かる
- 作業プロセスが非常に高度である
- オペレーションの内容量が過多である
- 生産条件の下、生産に時間が掛かる
Step② 特定した制約に最大限のパフォーマンスを付与
Step①ではまず、工程内の制約条件に直に働きかけ、最大限のパフォーマンスを付与できないか検討します。安易に外部から人員募集したり、設備投資をしたりせず、今あるリソースのなかで解決できないか模索します。
例えばスループットが他と比較して著しく低くなるほど、「スタッフのスキルが低い」のは、その工程にスキルが低いスタッフばかり集まってしまった結果とも考えられます。他の工程のスタッフとほどよく人員配置をして、各工程における作業員のスキルや習熟度が高・中・低とバランス良くなるようにしましょう。
そうすると自ずと、スキルが低いスタッフの習熟度も上がることが見込めます。また「作業プロセスが非常に高度」な場合、習熟度の高いスタッフを引き抜いても問題なさそうな工程班から人員を増やすという手段があります。
「オペレーションの内容量が過多」の場合は、無駄な作業がないかを見直し、ムダなオペレーションは排除・簡素化しましょう。オペレーションを減らせない場合は、「作業プロセスが高度」な場合の解決手段とは逆に、他の工程から習熟度が低いスタッフを割いて、軽作業を担当させる手段があります。
最後に「生産条件の下、生産に時間が掛かる」は、そもそも加工スピードが遅いという処理スピードに絡んだ問題があり、既存のリソース内での改善が最も難しい制約です。この場合、原料の搬入・仕掛品の搬出や品質チェックに資材係や品質管理部門からスタッフを派遣し、現場スタッフには生産に集中させるという手段があります。
但し、コミュニケーションコストが掛かったり、現場の稼働時間帯と他部門の就業時間が合わなかったりと、あまり良い解決策ではありません。そのためこの場合も、外廻りや工程内の準備・点検作業にムダがないかの徹底的な見直しから始めるケースが多いようです。
また可能であれば、ボトルネック工程で時間的に都合のよい数量分を加工する間に、他工程では全く別の製品を加工することで、時間的なロスを回避する手段もあります。但しこの手段を採ると、各製品の納期調整や資材・仕掛品搬入出が煩雑となるため、それに対応する資材係や生産管理の体制を整えなくてはなりません。
Step③ 他工程や工場全体でStep②に合わせて調整・従属
Step②で決定した人員配置換えや無駄なプロセスの排除を実際に行い、それを定着させ効果が確認できる検証期間を設けます。
決定内容によっては工程全体で人員の配置が変更されたり、ボトルネック工程で簡素化したオペレーションに合わせ前後の工程で何らかの調整が必要となったり、ボトルネック工程に適切な量の仕掛品を流すために他工程の生産量を減らしたり、全く別の製品を生産したりする必要があります。
そのようなStep②の決定内容に工場全体を従属させ、それに関わるさまざまな調整を行って、実際にボトルネックの制約を軽減できるか検証します。期間に関しては、習熟度が高いスタッフでも、新しい配属先の作業内容やスタッフ同士との連携など、勝手が分かり作業をこなせるようになるまで、少なくとも1週間は掛かると想定しましょう。
習熟度の低いスタッフの配置換えであったり、管理体制を新たに整えたりするなら、それ以上の検証期間やきめ細やかな調整が必要となるかもしれません。特に煩雑な処理に対応できる管理体制を設ける場合は、別途コストが掛かる可能性があります。次のStep④と比べてどちらが工場全体の運用や売上に益となるか、比較検討をしましょう。
Step④ 制約を物理的に解消|設備投資や人材育成
現状のリソース内でやれることを全て網羅した後に、大きな改善が見られない、もしくは更なる向上を目指したい場合、新たに資金を使って制約条件となっているボトルネック工程へのリソースを増やしましょう。
具体的には設備投資や人材育成となります。ボトルネック工程の設備・人材を現状の2倍投入すれば、単純に数字だけで見ると生産高も2倍になると見込めます。但し熟練工やリーダーの育成に時間が掛かかり、保全活動も2倍となるため、その分のコストも加味することが必要です。
とは言え、制約条件となっているボトルネック工程の生産能力の底上げは、工場全体にかかっていた制約を軽減し、全体の生産能力の引き上げに繋がります。
Step⑤ 他の制約を探し、①~④のプロセスを繰り返す
Step④までが完了すれば、新たに定常的なボトルネックとなっている工程や制約条件を見つけ、Step①~④を繰り返しましょう。
また既にStep④まで完了したボトルネック工程であっても、生産高や生産効率が目的に達していない場合は、再びStep①から仕切りなおす必要があります。この時、制約条件が解消しきれなかった要因を適切に究明して、同じことの繰り返しにならないように注意しましょう。
このようにボトルネック工程を最小限のリソースで最大限のパフォーマンスを付与することから始める5段階集中プロセスを用いることで、工場にかかる制約の可視化から解消までのマネジメントを効率よく合理的に行うことが可能です。
TOC理論のデメリット
もう古い?制約理論の欠点とは?
制約条件にフォーカスするTOC理論は、既存のリソースを最大限に有効活用できるマネジメント方式ですが、制約条件への注視と改善のみに偏ると次のような問題点が発生します。
- 制約条件に注視しすぎ、全体が見えない
- 制約条件の上辺のみ問題視し、根本解決に至らない
- 外部変化への対応力が乏しくなる
- スタッフに負担や抵抗感が生じる
ひとつの制約条件に注視し過ぎると、他の重要な問題点が見過ごされてしまうリスクが生じます。「5段階集中プロセス」のStep⑤で、前4段階を繰り返す際に必ず工程・工場全体を俯瞰的に見て、その他の問題点や制約の有無を確認しましょう。
次に制約条件の上辺だけ見てしまう場合、例えば「この工程は作業スタッフ全般のスキルが低い」のが制約条件と判断したとしても、それが必ずしも最適解とは限りません。
現場監督者の態度がかなり高圧的であったり、現場環境の温湿度が適切でなかったりと、根本的な原因が別にあるケースがあります。その場合、作業スタッフを入れ替えてもボトルネックの改善には至りません。その際には「なぜなぜ分析*3」などを活用し、ボトルネックの制約条件を正しく把握すべきです。
また「TOC理論が古い」と言われる最たる理由は、既存リソース内での改善・カイゼンに固執し、外部変化への柔軟性に乏しい体制に陥る可能性があるからです。
「働き方改革」による従業員の意識変化や、日進月歩する製造用機械の刷新や自動化、果ては組織そのものやビジネスモデル自体の変革を推進するDXなど、時流や外部の変化に対応できる柔軟性は常に求められています。
最後に、制約条件を解消するために作業員の配置変えやオペレーション内容の変更などは、作業スタッフの協力が不可欠であり、かつ負担を掛けることになります。なるべく抵抗感なく、円滑にプロセス段階を進めるためにも、スタッフへの説明責任や可能な限りの配慮を必ず行いましょう。
*3:「なぜなぜ分析」とはトヨタ生産方式から生まれた、トラブル分析方法。生産時や生産試験段階で問題やトラブルが発生した際に「なぜ?」と5回繰り返すことで、原因を徹底的に追及、洗い出す手法。再発防止や改善・カイゼン策を見つける際に役立つ。
TOC理論とトヨタ生産方式との違い
日本が誇る製造業の生産方式に「トヨタ生産方式(TPS)*4」があります。トヨタ生産方式はニンベンのある自働化*5とジャスト・イン・タイム*6を2本柱に、改善の積み重ねとムダ・ムラ・ムリを徹底的に省いた、顧客へ最短で良質な製品を届けるための生産管理システムです。
一方でTOC理論は生産管理システムとは異なり、製造業ではボトルネック工程の制約条件を解消するマネジメント手法として活用されています。
TOC理論の提唱者であるエリヤフ・ゴールドラットはトヨタ生産方式をはじめ、それに倣う日本の製造業を好んでいましたが、グローバルな視点での貿易関係を考慮し、TOC理論をはじめとするさまざまなマネジメント手法が提唱された自身の著書「The Goal」の日本語翻訳を17年間、禁止していました。
というのも、原書が出版された1984年当初に日本企業の経営者が「The Goal」を学べば、日本は大きく貿易黒字に傾き、かえってそれが日本経済にも世界経済にも打撃を与えると見越していたからです。
今ではさまざまな製造業でトヨタ生産方式に倣うのと同じく、ボトルネック工程の解決のためにTOC理論を用いる企業が増えています。
*4、5、6:TOYOTA公式HP「トヨタ生産方式」参照
「ジャストインタイム」について詳しく知る>>
「ニンベンの付いた自働化」について詳しく知る>>
ボトルネック特定にスマートマットクラウド
スマートマットクラウドはリアルタイム実在庫の見える化で在庫管理、工程カイゼン・DXを進めるIoT SaaSプロダクトです。IoT重量計で在庫管理・入出庫・発注を自動化。さらに現場でのモノの動きも捉え、工程間のモノの流れを分析し問題を見える化します。
シンプルな「重さの変化」をデジタル・ネットワーク化し業務変革に用いるDXとして、リアルタイム実在庫データを武器に、現場のさまざまなモノと情報を可視化し活用。工程をまたぐモノと情報の流れの澱みも特定します。
そのため複数工程におけるボトルネック工程の早期発見など、工場の生産高に直接かかわる制約の解消、生産効率や現場力の向上に寄与します。
さらにスマートマットクラウドは生産工程の各進捗状況も見える化。生産管理部門では上位の管理者システムにより現場の監視・コントロールを行い、また各工程の現場ごとに閲覧モニターを設置すれば、コミュニケーションコストを掛けることなく工場全体で工程の進捗度合いの把握が可能です。
後工程からひとつ前の工程に、必要な部品を、必要なタイミングで、いくつ必要かを自動で伝えることで、複数工程の生産プロセスに潜むさまざまな課題・制約の早期解消が行えます。
◆特徴
- 遠隔で在庫を一元管理:倉庫や各拠点の在庫を管理画面で一元管理
- 需要に見合った供給を実現:ひとつ前の工程に伝え、過不足なく生産できる
- 生産効率を最大化:リアルタイムかつ自動で伝え、ムダがない
- 仕掛品の流れを可視化:原料や仕掛品の滞留箇所や僅少箇所を早期検知
- 工程進捗の把握:コミュニケーションコストを掛けずに工場全体でモノの流れを把握
この記事を監修した人
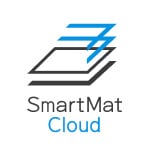
製造DX協会
製造DXに取り組む製造業・スタートアップ・エキスパートが集結し、企業の垣根を越えてノウハウを共有しながら社会全体に最適な製造DXガイドラインを発信しています。
https://manufacturingdx.org/