在庫管理術
倉庫×DX【製造業においてJITを成功させるカギとなる在庫管理とその事例】
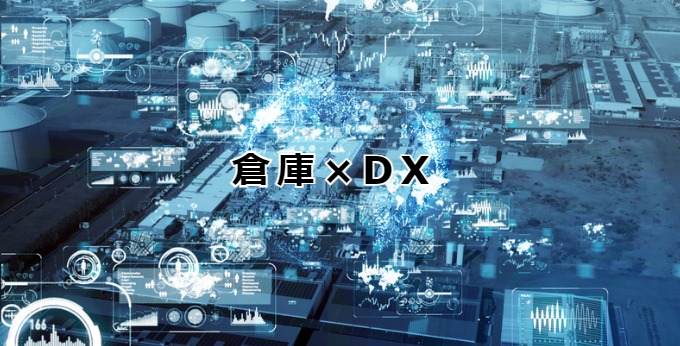
倉庫のDXとは?
ビジネス環境の激しい変化に対応し、企業が競争性の優位性を確立するために、データとデジタル技術を活用して、製品・サービス・ビジネスモデルの変革を実行しつつ、業務そのものや組織・プロセス・企業文化・風土を変革する「DX」*1。今やDXは顧客や市場のデータ分析や、製造現場のデジタル技術革新のみに留まりません。
「倉庫」におけるモノの流れや棚卸といった在庫管理にもDXの波が押し寄せ、高度なデータ処理能力を持つAIやロボットなどのデジタル技術を活用した、さまざまな在庫管理システムが登場しています。
倉庫には小売店舗に付属するバックヤード的な倉庫から、大規模な物流センターの倉庫、そして製造業では構内物流*2の一環として活用される倉庫など、利用目的に応じてあらゆるタイプの倉庫があります。
その中でも今回は特に、製造業の構内物流に用いられる倉庫にフォーカスを当て、製造業の倉庫DXにどのような在庫管理システムがふさわしいか、製造業に欠かせない生産方式の理念であるJIT*3に適した内容になっているかを検証していきましょう。
*1:経済産業省の「DX」における「デジタルトランスフォーメーションを推進するためのガイドライン」を参照
*2:構内物流とは、製造業の工場敷地内の物流のことであり、製造業務の効率化において重要な役割を占めています。
*3:ジャストインタイム、「必要な時に必要なモノを必要な分だけ」生産し在庫を徹底的に減らし、業務を効率化すること。もとはトヨタ生産方式の理念のひとつであり、さまざまな製造業において活用されている。
倉庫DXがもたらすJITへの成功の鍵
倉庫DXとは、生産段階における業務効率化・製品の品質向上や新しい価値が付加されることを最終目標とし、単純に倉庫内の在庫だけをデジタル技術を用いてデータ処理するだけに留まりません。
製造現場である工場全体の構内物流をリアルタイムかつ俯瞰的に見える化することで、過剰在庫によるコスト・倉庫面積の圧迫や、欠品による生産リードタイムの延長などを防ぎ、JITに即しかつQCD*4の向上を果たすレベルにまで生産効率を上げてこそ「倉庫のDX」が成功したと言えます。
では在庫やモノの流れに関してどのような課題を達成していけば、JITに即し成功した倉庫のDXと言えるのか、見ていきましょう。
- 倉庫内の在庫を遠隔かつリアルタイムで把握
- 現場各拠点のモノを遠隔かつリアルタイムで把握
- 入出庫などモノの流れを見える化
- 倉庫と現場の一時仮置き場など構内物流の見える化
- 液体・粉体などあらゆるモノの正確な実在庫の把握
- データ分析により欠品・過剰在庫を回避
*4:QCDとはQuality(品質)、Cost(コスト)、Delivery(納期)の略語。いずれも生産プロセスにおける重要な要素として位置づけられている。
実在庫を遠隔かつリアルタイムで把握する
倉庫内の在庫の種類・数量を遠隔かつリアルタイムで把握できれば、現物があるかどうか、数量に不足や過剰がないかを確認するために、わざわざ現場に足を運ぶことはありません。
また、各拠点の在庫をリアルタイムで把握できると、原料の補充遅延による生産ラインの停止や手待ちのムダ*5を防ぐことができます。さらに仕掛品や完成品で現場の一時仮置き場が溢れかえる、ということなく次工程の生産ラインなり、倉庫なり必要な場所に速やかに移動させることが可能です。
さらに倉庫・現場各拠点の在庫・モノを遠隔で一元管理することは、構内物流を俯瞰的に把握し、リアルタイムでの実在庫の把握に繋がり、常に適正在庫を維持しやすいというメリットがあります。
*5:手待ちのムダとはトヨタ生産方式で提唱される「7つのムダ」のうちのひとつ
入出庫管理・構内物流の見える化でムダを省き本業に集中
●購買・生産部門の管理者や現場作業員のムダを省く
二次元コードやRFIDタグ*6のスキャンで入出庫データを処理する、もしくは在庫管理システムのアプリを利用してスマホやタブレットで入出庫のデータ入力を現場で行うことができれば、紙を用いた入出庫伝票からの転記作業がなくなり、入力の際の労力や人的ミスをゼロにすることが可能です。
また出庫された原料や副資材は資材・購買の管理下から製造の管理下におかれますが、現場の各拠点でも倉庫と同じようにモノの管理をDX化することにより、現場の人間の労力削減し本業である生産への集中が可能となります。
その結果さまざまな動作のムダ*7を省けるため、生産リードタイム短縮による納期の前倒しや、現場のリソースに余裕がでることで生産ラインの異常や不良品の早期発見にも繋がります。
また仕掛品や完成品などのリアルタイムでの情報の共有は、各工程担当者や生産管理部門が工程間の進捗をコミュニケーションコストをかけることなく互いに把握できるという点がメリットです。もちろん生産関係者だけでなく、調達・購買部門や出荷オペレーターにも情報をリアルタイムで共有できれば、新たな原材料の調達や完成品の出荷作業にムダなく取り掛かることができ、調達リードタイムの短縮や納期保障にも繋がります。
入出庫管理をはじめ構内のモノの流れの見える化や、生産工程でのモノと情報の流れの停滞を排除し澱みなく流れる整流化によって、さまざまなムダが省かれ結果的に製品のQCDの向上に繋げることが可能です。
*6:RFIDタグとは電波を用いて非接触で情報を読み書きできる記録媒体。チップのような形状で、金属や水に弱いとされているが、近年では金属対応・液体対応のタグが登場している。二次元コードと異なる特徴は複数のモノを一括読み取りできる点と情報の書き込みが可能な点。
*7:動作のムダはトヨタ生産方式で提唱される「7つのムダ」のひとつ
●運搬要員のムダを省く
工程間のモノの移動、完成品の梱包・出荷など物流導線が多岐にわたる構内物流の運搬のムダ*8は、倉庫・各拠点におけるより正確な実在庫のリアルタイムデータによって省くことができます。
遠隔で一元管理している各拠点のデータに誤りや人為的ミスがあれば、原料の補充のためにわざわざモノを運搬してもまだ余裕があったり、実は別のモノの補充に迅速な対応が求めらたり、ということが発生します。これらが積み重なれば、人員不足やスペースの限界など、運搬業務の効率が著しく低下していきます。
もちろん物理的に運搬導線をスムーズにすることで、運搬のムダを省くことも重要ですが、消防法による保有空地の確保や建屋間どうしが離れている、工場構内が広すぎる、などの理由により運搬導線を物理的に変更することは非常にハイレベルな課題です。
そのため遠隔かつリアルタイムに倉庫や各拠点の実在庫データを正確に把握することは、構内物流である運搬作業を最小限にとどめる重要な要素となります。
*8:運搬のムダはトヨタ生産方式で提唱される「7つのムダ」のひとつ。
あらゆるモノを・あらゆる環境下で実在庫データを把握
製造現場で使用される原料には、車体のボディやモーターなど目視でもカンタンに数えられるものから、液体・粉体・小さなネジやワッシャーのように数えにくいモノがあります。
カンタンに数えられるモノは二次元コードやRFIDタグを貼りつけることも可能ですが、液体・粉体には二次元コードやRFIDタグを貼ることで種類分別はできても残量が分かり難い、小さなモノにはそもそもコードやタグが貼れない、というのが難点です。
また保管する原料の性質によっては冷蔵・冷凍保存が必要であったり、一時仮置き場の環境が水や金属を多用する現場の近くであったりする場合があります。
そのため、あらゆるモノをあらゆる環境下で正確な実在庫データを取得できるかどうかは、構内物流がスムーズに働く要点となります。
在庫の消費データ分析や発注点での自動発注or発注アラート
直接材となる原料の納入や入出庫による増減、完成品の出荷などあらゆるモノの流れや消費データがカンタンに分析できれば、適正在庫を保つための発注点を管理・更新することが易しくなり、また顧客の要望への対応や製品の需要変化を捉えることも容易になります。
それには納入や入出庫に関する転記作業が不要でデータが自動転送され、一元管理しているPC上で推移グラフへの処理がカンタンにでき、またさまざまなシステムや基幹系システムとの連携が可能なシステムが望ましいでしょう。
さらに発注点に到達すると自動で発注を掛ける、もしくは発注アラートを発信するなど発注タイミングが自動で通知されるシステムであれば、発注における人的負担も各段に削減されます。
倉庫×DXで生産効率を極める「スマートマットクラウド」
リアルタイムかつ俯瞰で構内物流を見える化し、高度な業務効率化を叶える倉庫のDXには重量センサを用いた「スマートマットクラウド」がおすすめ。緻密なセンシング技術を備える重量センサと、クラウドを介して遠隔&一元管理を可能にする高度で堅牢なデータ転送・処理能力、基幹系システムをはじめさまざまなシステム連携が可能なCSV、API技術、さらに高度な自動発注システム*9を搭載しています。
管理したいモノを重量センサに載せるだけでOK!二次元コードやRFIDタグを使用する在庫管理とは異なり、スキャンやタグ貼りに掛かる労力の削減・重さによりあらゆるモノの正確な実在庫データの把握が可能になります。
*9:予め決めておいた閾値を超えると発注先に合わせたさまざまな形態で自動発注が可能。自動発注を設定しない場合は発注アラート(発注タイミングとして自動で通知される)を出すことができる。
載せっぱでOK。正確なリアルタイムの実在庫データを転送
スマートマットクラウドは重量センサを用いた在庫管理・工程管理システムであり、Iot重量センサにより実在庫を計測し、クラウド上で実在庫データを記録し管理。リアルタイム実在庫データを発注や購買工程・在庫管理に活用できます。
また、SMCアプリを用いた入出庫管理から重量センサ同士を連携させて「モノの流れ」をデータとして取得・記録。生産工程の進捗具合を把握し、遅延・停滞のボトルネックを特定することができます。
ケーブルレスかつ省エネルギーで電池交換は約5年間不要!優れた耐久性と防滴仕様、かつ冷凍庫・冷蔵庫での利用も可能なので、置く場所を選びません。サイズはA6~A3を展開。限られたスペースでも柔軟に使用することができ、さらに重量センサを組み合わせたマルチマットで重量物の計測も可能。
倉庫や各拠点の在庫を把握するために工場内を走り回る必要はもうありません。膨大な在庫データやモノの流れの蓄積・分析により、適正在庫を保持し顧客対応にも役立ちます。
何よりも予め決めておいた重さの閾値を超えると自動で通知。在庫管理においては発注タイミングの通知や自動発注に至り、さらに生産工程においては補充品不足や工程間のモノの流れの淀みを発見しやすくなります。
工程間管理や生産準備、仕掛品の管理にも最適
JITを実現するためにかんばん方式や配膳作業といった生産方式が採用されていましたが、工程間や生産前段階でのモノの流れについても重量センサを利用することで、さらに業務効率が向上します。
IoT重量センサで現場のモノの動きを捉え在庫管理を自動化、その上で工程内のモノの流れを分析し問題を見える化します。さらにリアルタイム実在庫データを武器に工程を跨ぐ流れの澱みを特定しDX、現場力の向上に寄与します。
在庫置き場に出向くことなくリアルタイムで管理画面から部品と仕掛品の在庫数を確認できます。在庫確認や補充タイミング把握のため、倉庫や工場内を走り回る必要はもうありません。
スマートマットクラウドは生産工程の進捗状況も可視化。
後工程からひとつ前の工程に、必要な部品を、必要なタイミングで、いくつ必要かを自動で伝えることで、製造業の生産プロセスに潜むさまざまな課題を解消します。
◆特徴
- 遠隔で在庫を一元管理:倉庫や各拠点の在庫を管理画面で一元管理
- 需要に見合った供給を実現:ひとつ前の工程に伝え、過不足なく生産できる
- 生産効率を最大化:リアルタイムかつ自動で伝え、ムダがない
生産停止リスクを排除したスマートマットクラウド導入事例
スマートマットクラウドは、現在多くの企業様に導入いただいています。重量センサによる在庫管理で、欠品による生産ラインの停止リスクを排除した寄与した事例をご紹介します。
重量物も自動管理したスマートマットクラウド導入事例
パレットやコンテナで運搬するような数百kgもの重量物をSMCで自動管理することで、発注と在庫確認作業から現場作業員を開放した事例をご紹介します。