在庫管理術
ドカ停とは?定義やチョコ停との違いと関係性を解説
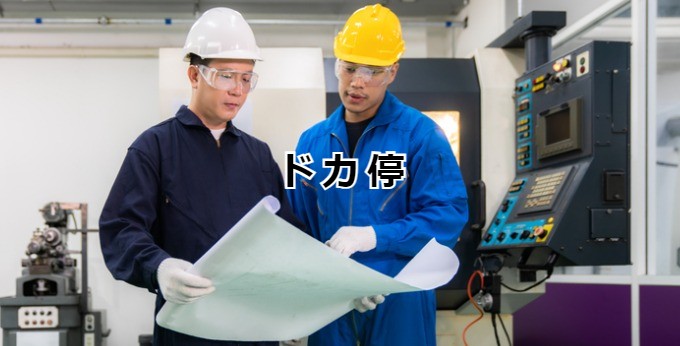
この記事では突発的な設備トラブルにより引き起こされる「ドカ停」について、くわしく解説しています。
残念ながらドカ停が生じた多くのケースで、設備の保全活動が適切であったとは言えません。しかし保全業務は技能継承者不足をはじめ、数多くの課題を抱えています。こちらでは、そのような保全業務をサポートするIoTソリューションをご紹介します。
ドカ停とは?定義をわかりやすく説明
ドカ停とは、生産ラインの装置・設備の突発的な故障により長時間にわたり生産がストップし「どかっと停止している状態」を表します。ドカ停はその略語で、製造業における設備管理用語のひとつです。
日本産業規格(JIS)における「故障」のなかで重大、または決定的な故障として「大故障」が登録されており、「ドカ停」はその通称とされています。JISでの定義は以下。
設備が次のいずれかの状態になる変化。a)規定の機能を失う・b)規定の性能を満たせなくなる・c)設備による産出物や作用が規定の品質レベルに達しなくなる。
備考:設備が生産ラインなどの大規模なシステムの一部となっていて、システム全体を停止に至らしめるような重大又は決定的な故障を大故障(通称としてドカ停)という。
日本産業規格(JIS)「生産管理用語」より引用
またライン停止から復旧にかかる時間の目安は、少なくとも1時間以上。より深刻な場合、自社保全スタッフの復旧作業では改善せず、設備や機械メーカーのスタッフを招請し修理・交換にあたるケースも。そうなると最低でも1~2日のダウンタイムが発生します。
このようにドカ停は「生産ラインがすぐさま稼動できない」のが特徴です。さらにひとたびドカ停が起こると、ダウンタイムだけでなく廃棄ロス・スタッフの手待ち時間などを含む生産ロスも発生します。
そのためドカ停は工場の大きな損失になるばかりか、企業経営にも影響する危険性を孕んでいることは否定できません。
ドカ停とチョコ停の違いと関係性とは?
チョコ停との違い
チョコ停は設備トラブル等で生産ラインが、「ちょこっと停止した状態」を表す略語です。JIS規格の生産管理用語で設備故障のうち設備小故障に分類され、その通称として登録されています。
チョコ停とドカ停の最たる違いは復旧に要する時間。ドカ停は1時間以上から日数を跨ぐ場合があるのに対し、チョコ停は数十秒から数分間であることが特徴です。
またチョコ停は現場スタッフのみで当面の解決が可能な設備トラブルであるのに対し、多くのドカ停は現場スタッフのみでは対応できません。重大かつ深刻な設備トラブルによるドカ停の解決には、少なくとも保全スタッフを巻き込まざるを得ない状況となります。
さらにチョコ停は時間ロスの少なさから工場の稼働時間範囲・設備7大ロスに含まれます。そのため工場稼働率を算出する際に、チョコ停を細やかなファクターとして計算に入れるのに対し、ドカ停は全くの計算外・完全ロスという扱いとなります。
チョコ停との関係性
チョコ停の多くは、設備稼働前の清掃不足や点検・保全作業不足によるコンタミ混入・設備不良となります。その設備不良もネジ・ボルトの増し締めを怠った、潤滑油を挿し忘れた、ゴミが装置に挟まったなど、軽微な原因による発生が少なくありません。
そのため重大かつ深刻な設備故障によるドカ停とチョコ停は対極にあると考えられがちです。しかしチョコ停のなかには、原因が曖昧であり、かつ同じような状況での生産ライン停止を繰り返すケースがあります。
例えば突発的な生産ラインの停止後、一通りの点検・保全活動を行い、はっきりとした原因が掴めなくとも、装置・設備を再起動させると問題なく稼働したとしましょう。そうなると現場スタッフは生産計画の遂行に重きを置くため、そのまま生産を再開します。
ただし原因が曖昧で頻発するチョコ停には、大きな設備異常が潜在すると考えられています。そしていずれは深刻なドカ停に繋がる可能性があるため、チョコ停といえど軽視しないようにしましょう。
生産を再開すること自体が悪いわけではありません。しかし原因が曖昧でかつ同じような状況でチョコ停が繰り返される場合、現場・保全スタッフが連携し、チョコ停の集計を取ったり、根本原因を探ったりすることは、ドカ停を予防する上で必要不可欠です。
ドカ停を防ぐには?
ドカ停を防ぐ保全活動
ドカ停を防ぐためには、日頃の保全活動や計画的メンテナンスが必要です。
大きな保全活動としては、
- 事後保全
- 予防保全
- 予知保全
の3つが代表的です。
事後保全には予想外の設備トラブルが発生した場合に対応する緊急保全を含みます。ただし保全活動の全てを事後保全にしている製造業は少ないでしょう。
また予防保全では、過去の故障履歴や機械消耗品の使用期限から、装置・設備それぞれのメンテナンス周期を割り出します。そして定期的に保全活動を行うことで設備トラブルを予防する保全活動です。
予知保全は設備保全のDXを推進する上で、新たに注目されている保全活動です。高度なセンシング技術で装置・設備の故障予兆を捉え、機械学習によって予め故障を診断するシステムを用います。
毎日、機械に触れている作業スタッフの視点も重要
これら保全活動をベースとして、最も重要なのは「ドカ停」を引き起こす前に設備異常に気づくこと。設備異常の早期発見には、日頃から機械を扱っている現場スタッフの視点も重要です。
機械稼働前に行う清掃や日常点検の違和感や異常の有無や、原因が曖昧かつ高頻度なチョコ停発生の有無は、現場のスタッフ目線でしか知り得ません。そういった情報がなるべく早く共有され保全・現場スタッフの連携が取れる体制が理想です。
反対に突発的故障が引き起こされ、「ドカ停」まで拡大しダウンタイムやロスが膨大となったとします。そういった場合は保全活動の体制が上手く機能していない、現場との連携が取れていないという指標になります。
保全品のストックやメンテナンス周期を見直すにしろ、故障診断など新たなシステムを導入するにせよ、自社の保全活動全般を見直すなら、その際には必ず“現場との連携”も取れる体制にしていきましょう。
関連記事を読む>>「保全管理」
関連記事を読む>>「設備保全 DX」
ドカ停を防ぐ保全活動の課題とは?
保全活動には、技能継承者不足や煩雑で膨大な保全品の在庫管理工数、生産が優先されるあまりに休業日や深夜・早朝に行われるメンテナンスなどの課題があります。
特に保全品が欠品していれば、ドカ停など突発的な設備トラブルに対する迅速な緊急保全を妨げます。結果的に、ダウンダウンタイムをさらに拡大することも少なくありません。そのような保全品の在庫管理の課題は以下の通り。
- 倉庫・現場各拠点に点在する保全品の棚卸・在庫管理が煩雑。巡回必要
- 消費スピードが読みにくい消耗品の発注は人の経験や勘頼み
- 旧式となった機械予備品の不動在庫化の識別が困難
- 使用用途が不明・属人化した保全品の整理・整頓が困難
- ネジ・ボルト・ベアリングなど目視では正しいカウントが困難
- メンテナンス工具も現場各拠点に点在、または紛失
このような保全品の在庫管理の課題は、IoT重量計によるリアルタイム在庫管理システムで解消することが可能です。
欠品が生産ライン停止と直結する機械消耗品管理の課題解決を見る>>
さまざまな緊急保全に必要な保全品の在庫管理を効率化する方法とは?
IoT重量計を使用すれば、各拠点に点在した機械消耗品やメンテナンス工具の在庫を遠隔で一元管理できます。また重さの変化により消費履歴データを分析し最適発注点や閾値を提案。人の経験や勘に頼らない適切なデータに基づいた発注が可能です。
さらに重さによって個数を正確にカウントするので、数えにくいネジ・ボルト・ベアリング・潤滑油などの液体も正しく把握。リアルタイム在庫データによりさまざまな在庫管理工数を削減します。
また複雑にカスタマイズされた装置や機械や長年使用している設備はメンテナンス自体がどうしても属人化しがち。それに伴い、予備品やパーツの在庫管理も担当者任せとなっている現状をIoT重量計による在庫管理で解決します。
ドカ停の時間短縮を可能に!保全品の適正在庫維持に貢献する「スマートマットクラウド」
スマートマットクラウドはリアルタイム実在庫の見える化で在庫管理、工程カイゼン・DXを進めるIoT SaaSプロダクト。IoT重量計を用い、管理したいモノをマットに紐づけて載せておくだけで、重量変動を計測しクラウドを介してデータを上位システムに転送します。
スマートマットクラウドはこのようにシンプルな「重さの変化」を捉えてデジタル・ネットワーク化し業務変革できるDXを実現。リアルタイム実在庫データを武器に、倉庫や各拠点に点在しているさまざまな保全品の情報を可視化し活用できます。
入出庫などの在庫管理はもとより、適正在庫を維持するための自動発注が定期・定量発注方式双方で可能。また過去の消費履歴や発注履歴の収集データ(2ヵ月分)をもとに最適閾値や発注点を提案します。
数えにくいモノ・液体も重さにより正確にカウント。スマートマットはサイズ展開も豊富でg単位からマルチマット使用で数百kgまで対応します。機械予備品の不動在庫化や機械消耗品の過剰使用も消費データ(2ヵ月分)の学習ロジックによりリコメンド。
保全品の在庫管理や発注における属人化を脱却し、さらに管理工数を大幅に削減します。棚卸のために各拠点を探し回ったり、使用用途が不明なストック品に頭を悩ますことはもうありません。
さらには保全品の適正在庫の維持や保管所在地の把握により、ドカ停などの突発的な設備トラブルへの早期対応が可能でしょう。
◆特徴
- 突発的な設備トラブル対応:保全品の適正在庫の維持や所在地の把握により早期対応可能
- 遠隔で在庫を一元管理:各拠点のリアルタイム在庫データを上位システムで一元管理
- 適正在庫を維持する自動発注:人の経験や勘に頼っていた属人化を脱却
- 重さによる正確なカウント:数えにくい消耗品(ベアリング・潤滑油)の管理工数削減
- 用途が曖昧なストック品の顕在化:整理しマットに紐づけ。不動在庫化にも早期対応
この記事を監修した人
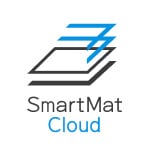
製造DX協会
製造DXに取り組む製造業・スタートアップ・エキスパートが集結し、企業の垣根を越えてノウハウを共有しながら社会全体に最適な製造DXガイドラインを発信しています。
https://manufacturingdx.org/