在庫管理術
設備保全×DX【失敗しないDXのための予知保全システム+保全品管理システム】
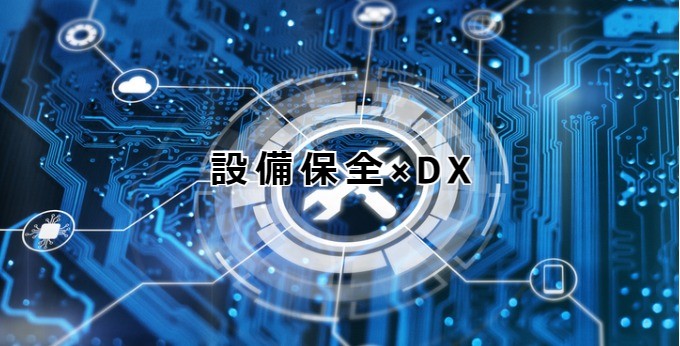
この記事では、設備保全をとりまく現状や課題を解説。昨今の設備保全には、高度なセンシング技術やAI学習機能を用いた予知保全システムが、設備保全のDXに必要だと声高に言われています。
では、どのような導入段階を踏めば「失敗しないDX」ができるのかを分かりやすくご紹介。自社の設備保全変革に課題感をお持ちの方はぜひご一読ください。
設備保全を取り巻く現状と課題
取り巻く現状|高度なオートメーション化&複雑な需要対応
近年の製造業では、オートメーション化がますます進んでいます。単純作業や重量物の搬送だけでなく、精緻な熟練工の技術がロボットアームで再現可能となったり、ひとつずつ目視で品質確認していたのをプロセス内検査機で監視可能となったりしています。
それだけではなく、変化の激しい消費者ニーズに応えるため、マスカスタマイゼーションや多品種少量生産・変種変量生産といった生産体制にシフトしていく製造業が数多くあります。
その結果、生産現場の装置・設備は高度かつ精密であり、また搬送システムやユニット構造・ライン構造なども多種多様かつ複雑化しているのが現状です。そのような中、設備や装置に故障が発生すれば稼働率の著しい低下に直結します。
そのため設備・装置故障の未然防止や、経年劣化が見られる設備・装置を修繕、交換する保全活動は欠かせません。さらにますます高度化する設備・装置をメンテナンスする保全スタッフにもハイレベルな技術が要求されています。
課題|設備保全はDXに取り残されがち?
製造業のDXやインダストリー4.0*1が謳われる時流のなかで、IT技術や顧客データを最大限に利活用し、競争の優位性の将来的な持続のために、さまざまな変革・改革が製造業で行われています。その最たる理想像としては「スマートファクトリー」が挙げられるでしょう。
ただ生産ライン全体はDXの波に乗り、スマートファクトリー化しているのに、保全活動は従来と変わらないということも。エクセルで故障履歴を集計し、そこから予防保全のメンテナンス周期を算出している、保全品の購入タイミングを人の経験や勘で決めているなど、アナログ感がぬぐえない状況から脱していないケースがあります。
しかしながらオートメーション化が進んだ工場では、突発的な故障やトラブルが工場収益に限らず企業経営までクリティカルな打撃となる可能性が増大しました。そのため設備保全にも、最新のIT技術や多様なテクノロジーを用いた「予知保全」をDXの一環として採用する流れが見られます。
*1:インダストリー4.0とはドイツで提唱された第4次産業革命のこと。製造業によりIT技術を取り入れ、改革を目的とするもの。
関連記事>>「製造業のDX」
関連記事>>「インダストリー4.0」
予知保全とは?わかりやすく解説
設備保全には次のように、
- 事後保全(BM / Breakdown Maintenance)
- 予防保全(TBM / Time Based Maintenance)
- 予知保全(CBM / Condition Based Maintenance)
の3つが代表的な保全活動として挙げられます。
事後保全と予防保全
「事後保全」とは装置・設備に故障が発生してから修理や交換を行う保全活動です。突発的な故障やトラブルに対応する緊急保全は事後保全の範疇に入ります。ただし通常の保全活動が事後保全ならば、あらゆる保全品や予備品をストックするため、在庫スペースやコストを圧迫します。
また事後保全の特性上、保全スタッフは現場が稼働しているなら、夜間や休日でも呼び出される可能性が著しく大きくなります。さらに計画外の生産ライン停止での故障対応となるため、稼働率や納期への影響も大。事後保全を通常の保全活動に採用するのは、メリットが余りにも少ないと言えるでしょう。
「予防保全」は保全活動の中で、最も多く採用されている保全活動です。時間基準保全(TBM)とも言われ、過去の故障履歴や部品の耐久性などから予め設定した周期に基づき、定期的にメンテナンスを行います。
但し予防保全を用いたとしても、突発的な故障を皆無にすることはできません。また反対に、必要以上にメンテナンス周期が短い、耐久性に支障がない装置や部品の交換など、不要なメンテナンスが行われており、コストや保全活動の負担増となる可能性があります。
予知保全とは?
「予知保全」とは予兆保全と同義で、装置や設備の状態に応じてメンテナンスを行う保全活動です。そのため状態基準保全(Condition Based Maintenance)、略してCBMという用語を使用。但しTBM、CBMともに「予防保全」に含む考え方もあります。
CBMは高度なセンシング技術により装置・設備の僅かな異常を検知し、AI学習で故障の予兆を診断するシステムを活用。さらに上位システムにデータを転送するIoTの搭載など、さまざまなテクノロジーを用います。
これらの技術で装置・設備に不具合や故障が発生する前のタイミングを捉え、事前に保全活動を行えるようにします。定期メンテナンスよりも最適なタイミングで保全活動が行えるため、保全品やメンテナンスに掛かるコストや人的負担の減少に繋がります。
またトラブルの予兆を捉えるため、突発的な故障抑制が可能です。昨今の製造業では、緊急保全や定期的なメンテナンスに加え、予知保全を取り入れる傾向が数多く見受けられます。
設備保全DX成功のための「CBMテクノロジー」&「人材」を詳しく解説
センシング技術
装置・設備の異常の予兆を捉えるセンサーや監視装置には次のような種類があります。
- 振動センサー
- 温度センサー
- 電流検出器
- 絶縁抵抗・抵抗値監視機器
特に代表的な「振動センサー」は、装置・設備の駆動部分の振動周期を測定するセンサーです。直動・回転駆動それぞれに専用センサーがあり、正常運転時と異なる振動周期を検知すれば、装置・設備異常の予兆を捉えたと考えられます。
本来、駆動部分の振動周期を正しく捉えるのは、筐体や接合部分の振動や共鳴にも感応してしまうため困難だとされていました。しかし近年ではこういったノイズをキャンセルし、駆動部分の振動のみを正しく捉えるセンサーが数多く登場しています。
また動作中の装置・設備は、摩擦熱をはじめさまざまな温度上昇の要因があります。温度上昇によって絶縁帯やベルト*2が破損し、異常停止のリスクが生じることも。温度センサーを用いた機械温度の危険区域監視により、トラブルの予兆を捉えます。
電流検知器は機械内を廻っている電流を測定するセンサーです。基本的に機械は定格電流値*3があり、それを超えるようならば何らかの異常や過負荷があるということ。そのため電流データを測定することで、機械の過負荷の早期検知が可能です。
また絶縁抵抗値や抵抗値の監視も有効です。絶縁帯が劣化すると電流が漏洩したり、電線や金属コイルの酸化が進むと断線が発生したりします。これらの予兆を捉えるためにも絶縁抵抗値や抵抗値を監視するセンシング技術が用いられます。
*2:タイミングベルトやコンベアベルトなど、機械のパーツ同士を連動させるための部品
*3:装置・設備を安全に使用するための電流の上限値
AI学習機能
初期の予知保全システムではAI学習機能が付随しておらず、センサーから転送されるデータが閾値を超えれば「故障の予兆」と捉えられていました。この閾値は過去の故障データから人間が考える必要があり、非常に難易度が高く、システムの導入失敗に至ったケースもあります。
そのため機械学習をするAI学習機能が実装され、データ解析やアルゴリズム構築をもとに故障診断ができる予知保全システムが主流となってきています。
監視システムと監視体制
AIだけでなくIoTを搭載している予知保全システムが故障診断すれば、その診断データを上位システムに転送します。そしてほとんどの予知保全システムでは、故障診断データをトリガーとして何らかのアラートが発信される仕様となっています。
但しそれが上位システムだけなのか、保全スタッフが携帯する端末にもアラートが届くのか、正しく把握することは必要です。またアップセルを行えば、アラートを受け取る端末を増やせるというケースもあります。
アラートが届く範囲により、上位システムのモニターに常時だれかを配置すべきか、そうでないのかで監視体制が変わります。さらに人件費だけでなく、保全スタッフの日々の活動導線にも影響があるでしょう。
また監視そのものをシステム側で請け負っている会社もあります。監視システムによっては、保全スタッフの勤務体制を見直す必要があるので、監視システムの詳細も必ずチェックするポイントです。
人材育成
そもそも機械保全には、機械保全技能士*4と電気工事士*5の資格が必要です。ただし資格に限らず、複雑にカスタマイズされた装置や、長年にわたり修理しながら使用している機械などは、図面があったとしてもメンテナンスが属人化している場合があります。
そのうえ目の前の保全活動に追われて、修理・交換・メンテナンスで何かしら特化した技能継承に費やすリソースが割けないケースも。そういった場合には、予知保全システムの導入に合わせて、人材育成プログラムが組み込まれているシステムを選んだほうがよいでしょう。
*4:公益社団法人 日本プラントメンテナンス協会のホームページより、機械保全技能士とは、メンテナンス技能を証明する国家資格のこと。
*5:電気工事士とは、電気工事士法に基づく国家資格のこと。資格を有さなければ電気工事・保守・点検することが許可されていない、いわゆる業務独占資格となる。
導入サポート+アフターサービス
予知保全システムは高度なセンシング技術やAIを活用するため、導入側で人材のリソースが割けない、プロフェッショナルなレベルの知識や技術がないケースは少なくありません。
例えばセンサーを選び、取り付け箇所ひとつ特定するにもハイレベルな知識と技術が必要です。適切な種類・取り付け位置でないと精度の高いデータは得られず、アルゴリズム構築にも支障をきたします。
そのため予知保全システムを販売する企業は、ほとんどが導入サポートスタッフを提供しています。なるべく手厚いサポートを実施している企業を選ぶのがベストです。
導入後もAIが提示する故障診断に違和感がある・過剰もしくは精度の低いアラートが来るという場合、センシングやアルゴリズム構築の元データから見直す必要があります。また導入後、すぐに瑕疵が判明するわけではなく、数ヵ月から1年以上かかって適正ではないと判明することが多いようです。
アフターサービスとして補償期間だけではなく、ある程度の費用を支払ってでも長く付き合ってくれるのかを見極め、契約書にもそういった事項を盛り込んでおく必要があるでしょう。
設備保全DXのための導入STEP
失敗しない設備保全DXのために、予知保全システムを導入する各Stepを紹介します。また設備保全DXをひとつのプロジェクトとして発足させ、責任者を明確にしておくのもDX推進のカギとなるでしょう。
Step① 課題整理とデータ確認
設備保全のDXを進める前に、まずは自社の設備保全の課題を以下のポイントで整理しましょう。
- 突発故障を繰り返す装置・設備の有無
- 突発故障のダウンタイムを算出
- 突発故障のロスを算出
- 複数の生産ラインには優先順位*6を格付け
- 装置・設備の正常時データの収集
- 装置・設備ごとの故障データの収集
- 各保全スタッフの技能・経験の確認
- 保全品の在庫管理状況
突発故障を繰り返す装置・設備が有るならば、メンテナンスに問題があるというより、機械可動時の負荷が装置・設備の能力を超えている可能性があります。そのような場合は、耐荷重や耐摩耗性・定格電流値などの性能がより高い設備・装置に交換しましょう。
メンテナンスの課題だけに整えた状態にしてから、設備保全の課題整理をします。まず突発故障時のダウンタイムやロス(製品廃棄ロスを含む)を算出しましょう。これは後に、システム導入の費用対効果を算出する際に重要になってきます。
また生産ラインを複数保持しているなら、ロスの大きさ・生産製品の重要度ごとに優先順位を着けましょう。こちらも後にスモールスタートでの効果検証や本格導入の際の横展開に必要となります。
また装置・設備の正常時のデータや故障データ*7は、予知保全に関するアルゴリズム構築の足がかりとなる情報です。ただしこういった情報が無くとも、ゼロベースからシミュレーション作成しアルゴリズムを開発する予知保全システムはあります。
また保全スタッフの技能や経験、それが継承できる企業風土かどうかを確認しましょう。また保全品の発注先・調達リードタイム・在庫数量が正しく管理できているかも、円滑な予知保全を行うためには見過ごせないポイントです。
*6:基本的にはロスの大きさで決定。他にもOEM専用生産ラインや短納期生産など複数軸で決めることもある。
*7:予防保全として常に安全圏で定期メンテナンス・交換を実施しており、故障データが極めて少ないという工場・生産ラインも多い。
Step② 予知保全システムの選定
予知保全システムの選定のポイントは、
- 少なくともセンシング技術+AI故障診断があるか
- 自社データが少ないなら、それに対応できるか
- どのような監視システムか
- 技能継承のプログラム・サポートがあるか
- 導入サポート・アフターサービスの実態はどうか
となります。以上のポイントを踏まえて、予知保全システムの選定は1社に絞らず、少なくとも3社以上は比較検討しましょう。
まずセンシング技術だけでなくAIによる故障診断の有無は、人的負担の削減とより正確性の高い故障診断のために不可欠です。
また自社の故障データがほとんど無い、そもそもセンサーでデータ採取したことが無い、という工場も少なくないでしょう。その場合、ゼロベースから機械アルゴリズムが構築されるまでのサポートがあるかどうかも大切なポイントです。
次に、どのような監視体制が必要なのか内容も把握しましょう。前述したように、保全スタッフの勤務体制に影響する可能性があります。勤務体制の変更がムリなくできるのか、人件費が大幅に上がらないか併せて考える必要があります。
また予知保全システムを導入すれば、時間基準保全が軸である予防保全と比べて定期メンテナンスやスケジュール調整に追われることが少なくなります。その余暇時間を使って修理・交換・メンテナンスなどの技能継承に当てることも可能です。
しかし保全スタッフ全体の技能底上げが必要であったり、スタッフ同士のコミュニケーションに支障があったりするなら、人材育成プログラムを利用したほうがよいでしょう。
これらのポイントについて資料を参考にするだけでなく、カスタマーサービスで丁寧に回答してくれるかどうかも、システム会社の企業風土を推し量る目安となります。
特にAI活用し故障判断までアルゴリズム構築させるには、専門家のサポートが必要不可欠。自社に合ったシステム会社を数社絞り込んだ上で、各社でスモールスタートから始め、適正かつ丁寧なサポートを行ってくれるか見極めましょう。
Step③ スモールスタートのための検証箇所選定
Step①で優先順位をつけた中から、中程度以下の生産ラインでスモールスタートするのがおすすめ。なぜなら優先順位が高い生産ラインを選定した場合、予知保全システムが上手く作動せず故障が発生すれば、工場の生産高に深刻なダメージを与える可能性があるからです。
一方で、余りにも優先順位が低く、稼働状況が続かないような生産ラインもおすすめできません。効果検証に長い時間を要したり、稼働し続ける生産ラインの機械アルゴリズム構築と乖離したりするケースがあるためです。
そのため、日々稼働しながらも計画外のライン停止が発生しても、クリティカルな状況に陥らない生産ラインから装置・設備を選定します。さらに予備品もストックした状態でスモールスタートを切るのがベストでしょう。
Step④ 効果検証
Step③まで終われば、スモールスタートの効果を検証しましょう。故障予兆が本当に正確かどうか、予兆・故障診断からデータ推移を確認しつつ故障が発生するまでの期間やデータ変動を確認する必要があります。
予兆から故障発生までの期間・データ変動により、診断の閾値やタイミングなどアルゴリズムの構築が正確か検証します。必要ならアルゴリズムに手を加えることもあるため、その際にシステム会社の協力が適切に得られているかどうかは重要です。
また人材育成や導入サポートという観点で、予知保全導入のプロジェクトチームだけではなく、他の保全スタッフや日常点検を行う生産現場スタッフの意見も聞いたほうがよいでしょう。プロジェクトチームには適切に対応していても、その他のスタッフへの対応が疎かだったりすると、本格導入後のサポートに不安要素が残ります。
Step⑤ 見積比較・導入を展開
最後に、各社の見積りを横展開やアップセルした場合を含めて、比較検討しましょう。どれほどよいシステムでも費用対効果が無ければ経営側は導入に前向きになりません。「今までどおり、現場が頑張ればよい」という結論に至る可能性があります。
設備保全のDXとして状態基準保全である予知保全を取り入れることで、ムダな定期メンテナンスや部品交換のコストがどれほど省けるのか数字で説明します。また技能継承など数字で表し難い部分にも、属人化の危険性などにフォーカスを当てましょう。
そして各社のシステム・サポート内容・見積り・検証結果を提示し、その中から最適解を選んだ理由を説明するのがベストです。システム導入が承認されれば、優先順位が中程度の装置・設備から上下に導入を拡大していくのがよいでしょう。
保全品の管理はどうする?DXできる?
保全品には大きく分けて、
- 機械予備品
- 機械消耗品
の2種類があります。機械予備品とは装置・設備の本体やパーツのこと。主に機械の筐体*6や接合部のパーツ、直動や回転部分の駆動部分がそれに当てはまります。また組立の際に使用する治具も機械予備品のひとつです。
一方で機械消耗品は、機械を円滑に駆動させるために必要なベアリングや円滑剤、生産環境のクリーン度を支えるHEPA/高性能フィルター、液体循環させるためのホースや漏れを防ぐコーキング剤が挙げられます。
機械消耗品の中には、樹脂硬化に使用されるUVランプや半導体の精緻なフォトレジストに使用されるような特定の波長を出す光源ランプもあります。これらは耐使用時間を超えると照度が落ちるなど、管理面での取り扱いにも注意が必要です。
*6:筐体とは、何かしらの機能を持つ電子機器や機械を収める箱やそれを覆うモノ
保全品管理が抱える課題
機械予備品は機械そのものを交換したり、型番が刷新された場合、それまで使っていたパーツが型落ちとなり使用できなくなるケースも。その場合、そのようなパーツは不動在庫となり在庫スペースやキャッシュフローを圧迫しがちです。
また、機械消耗品は倉庫以外にも生産現場の各拠点に点在して保管されていることが多く、さらに消費スピードが読みにくいというのが在庫管理におけるデメリットとなっています。
このような保全品の在庫管理の課題解決に、IoT重量計を用いた「スマートマットクラウド」が活躍します。
保全品の管理はIoT重量計でシンプルにDX!「スマートマットクラウド」
CSV編集機能やAPI連携・webhook搭載でさまざまな予知保全システムと連携可能な在庫管理システム「スマートマットクラウド」。IoT重量計にモノを載せるだけで、リアルタイムの重量変動データをクラウドを介して上位システムに転送します。
初期設定はIoT重量計(スマートマット)のシリアルナンバーとモノの情報(商品コード・商品名・1個/1袋当たりの重さ)を紐づけるだけでOK!スマートマットはサイズ展開も豊富でg単位からマルチマット使用で数百kgまで対応します。
閾値を下回った時の定量発注、もしくは在庫が減った分だけ発注する定期発注など、さまざまな発注を自動で行ってくれます。さらに過去の履歴データを学習し最適閾値や発注点を提案。
限られた保全要員だけではなかなか手が回らない、機械消耗品や予備品といった保全品の在庫管理や発注の自動化に寄与します。データ分析により機械消耗品の消費スピードを見える化し、発注点・閾値の最適解を提示。また各拠点に点在している消耗品をIoT重量計で一元管理することが可能です。
また装置や設備の刷新や型番の変更により、それまで使っていた予備品やパーツが不要となり、不動在庫化することも。そういった手が回りにくい保全品もIoT重量計で管理して置けば、不動在庫化を検知しお知らせ。キャッシュフローの正常化にも寄与します。
発注残管理や重複発注防止機能・学習機能など高度な情報処理能力を備えながらも、直感的で使いやすい管理システムと、「重量変動を検知する」というシンプルなプロダクトであるIoT重量計。
このIoT重量計を用いたスマートマットクラウドを使って、まずは保全品の在庫管理DXを達成してみませんか?
◆特徴
- 遠隔で在庫を一元管理:倉庫や各拠点の在庫を管理画面で遠隔かつ一元管理
- 自動発注:消費スピードが把握しきれない機械消耗品は自動発注で適正在庫を維持
- 不動在庫の検知:設備・装置の刷新や型番変更により、不動在庫化した保全品を検知
- シンプルなシステム:重量変動のリアルタイムデータをもとに分かりやすいシステム

空港を維持管理する膨大で煩雑な保全品の在庫管理をスマートマットクラウドでDXした導入事例
スマートマットクラウドは、現在多くの企業様に導入いただいています。スマートマットクラウドのリアルタイムIoT重量管理と自動発注で、手動管理では非効率であったさまざまな保全品の在庫管理をDXした事例をご紹介します。
この記事を監修した人
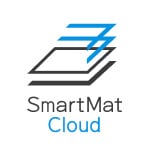
製造DX協会
製造DXに取り組む製造業・スタートアップ・エキスパートが集結し、企業の垣根を越えてノウハウを共有しながら社会全体に最適な製造DXガイドラインを発信しています。
https://manufacturingdx.org/