在庫管理術
安全在庫とは|計算式・求め方・メリット・最適な在庫管理まで徹底解説
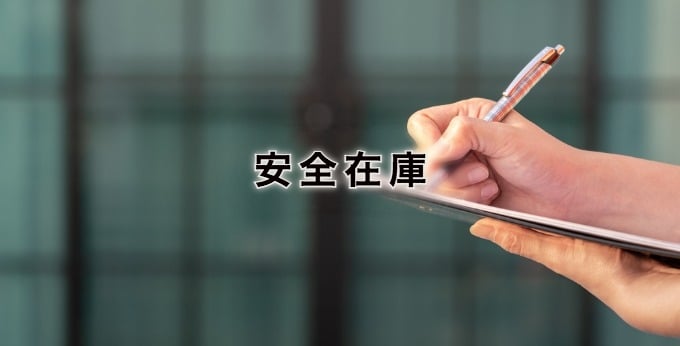
現代のビジネス環境において、効率的な在庫管理は企業の競争力を左右する重要な要素となっています。特に供給チェーンの不確実性が高まる昨今、適切な在庫水準を維持することは経営課題の一つです。
この記事では、在庫管理における核心概念である「安全在庫」について詳しく解説します。
\耳から学ぶ👂ポッドキャスト/
🎵音が流れます
安全在庫とは
安全在庫(英語:Safety stock)※1とは、需要の変動や供給の遅延など予測困難な事態に備えて、通常の在庫に加えて保持する予備の在庫を示します。具体的には季節変動やトレンド、キャンペーンなど不確定な需要変動への考慮や正確な納品リードタイムの把握、在庫コストとのバランスを見て、最低限保有すべき在庫量を設定します。
適切な安全在庫の設定により、欠品リスクを軽減し、顧客満足度の向上や販売機会の損失防止に繋がります。
※1:JIS規格では「需要変動または補充機関の不確実性を吸収するために必要とされる在庫」と定義されている。
安全在庫の計算方法と求め方
安全在庫は、以下の計算式で求められます。
安全在庫=安全係数※2×使用量の標準偏差×√(発注リードタイム+発注間隔)
実際の業務で適切な在庫管理を行い、欠品リスクと保管コストのバランスを最適化するには、計算式の各要素を的確に理解し、取り扱うことが必要です。この式で使用される各要素について、詳細を以下に説明します。
※2:安全係数は安全在庫係数とも表される。
安全係数(安全在庫係数)
安全係数とは、欠品許容率に基づく係数で、欠品リスクをどの程度まで許容できるかを示す数値です。
例:100個の注文に対し90個しか供給できない場合、欠品率は10%となります。欠品許容率に応じて安全係数は異なり、欠品許容率が高くなれば高くなるほど、安全係数は低くなります。
統計的に有意とされる数値は、欠品許容率5%の場合で安全係数は1.65がしばしば使用されます。欠品許容率に対する一般的な安全係数の数値は以下。
欠品許容率(%) | 安全係数(安全在庫係数) |
0.1 | 3.10 |
1.0 | 2.33 |
2.0 | 2.06 |
5.0 | 1.65 |
10.0 | 1.29 |
20.0 | 0.85 |
30.0 | 0.53 |
また、Excelの「NORM.S.INV」関数を利用して、次のように計算することも可能です。
安全係数 = NORM.S.INV(1ー欠品許容率)
使用量の標準偏差
使用量の標準偏差は、過去の出荷量や販売量のばらつきを示す指標です。商品の需要の変動を判断でき、過去の使用量(需要量)の平均からのバラつきを数値化しています。
この標準偏差により、過去の需要の変動を把握できるため欠品の防止に役立ちます。
標準偏差は、Excelの「STDEV」関数を利用すると簡単に求めることができます。セル範囲に入力されたデータに対して「=STDEV(範囲)」と入力するだけで、標準偏差を正確に計算でき、これにより、複雑な統計計算を手軽に実現することが可能です。
発注リードタイム
発注リードタイムは、仕入先に発注してから実際に納品されるまでの日数を指します。
例えば3月1日に商品を発注した後、3月10日に商品が納品された場合は、リードタイムは9日になります。
発注間隔
発注間隔は、一度発注した後、次回同じ商品を発注するまでの期間です。この数値を含めることで、在庫が完全にゼロになる前に発注するリードタイミングを加味できます。定期発注の場合はその周期、随時発注の場合は「0」となり、スケジュールを組む際に重要な指標となります。
安全在庫の実際の計算例
例えば、欠品許容率5%(安全係数1.65)で以下のような条件の場合、
- 欠品許容率5%(安全係数は1.65)
- 使用量の標準偏差:30
- 発注リードタイム:3日
- 発注間隔:7日
計算式に当てはめると:
安全在庫 = 1.65 × 30 × √(3+7)
安全在庫 = 1.65 × 30 × √10
安全在庫 = 1.65 × 30 × 3.16...
安全在庫 ≒ 156
結果、156個が安全在庫となります。このように、需要変動や供給の不確実性を考慮した在庫数を計算式によって確保することができ、欠品リスクを抑えることが可能です。
安全在庫と適正在庫の違い
安全在庫に似た用語に「適正在庫」があります。一見、同じような用語ですが、実際は異なります。
安全在庫と適正在庫の違いはWEBサイト「在庫管理110番」のコラムにて、下記のようにわかりやすく解説されています。
安全在庫とは、欠品を防ぐための在庫の下限値です。
適正在庫とは、在庫数の下限だけではなく、上限も決めて過剰在庫も防ぐことです。
引用:在庫管理110番「安全在庫の計算方法と設定の注意点」 閲覧日2024年4月10日
安全在庫は、欠品を防ぐのが目的で設定され、在庫数の下限を決めるもの。一方、適正在庫は、企業が利益を出すことを目的とし、在庫の下限だけでなく上限も決めるのが特徴です。
適正在庫の計算方法は、安全在庫にサイクル在庫(発注して次に発注するまでの間にどれぐらい在庫が消費されたのかを表す数値)もプラスします。
安全在庫のメリットと目的
安全在庫の目的
安全在庫を保有する目的は、企業活動におけるリスク軽減とサービス向上の実現です。具体的にいうと、
- 欠品リスクの軽減:需要の急増や救急遅延に備え、顧客への安定供給を維持
- 販売機会の損失防止:在庫切れによる販売機会の逸失を防止
- サプライチェーンの安定化:供給の不確実性に対応し、全体物流を円滑化
などが主な目的になります。
安全在庫のメリット
実際に、安全在庫管理を徹底した企業は、欠品による販売機会損失を最小限に抑え、安定した収益を維持しやすくなります。具体的なメリットとして、
- 顧客満足度の向上:安定した商品供給により、顧客の信頼を獲得
- 在庫管理の効率化:適切な在庫水準の維持により、在庫コストの最適化が実現
- 業務の標準化:在庫基準の明確化により、属人化排除と業務平準化を実施
このように正確な安全在庫の算出とその徹底は、経営の基盤強化に直結する施策と言えるでしょう。
安全在庫のデメリットと注意点
一方で、安全在庫には運用上の課題や注意点が存在します。そもそも安全在庫を正しく設定できない場合、企業の経営資源に負担を与える可能性があります。
- 過剰在庫のリスク:安全在庫を過大に設定すると、在庫コスト増加や滞留在庫発生に直結
- 欠品の完全防止は困難:予測不能な需要変動により欠品が発生する可能性も
- 定期的な見直しが必要:需要の変動や供給状況の変化に応じて、安全在庫の再計算は必須
- 正規分布の前提:安全在庫の計算式は需要が正規分布に従う※3ことが前提で、運用には注意が必要
※3:安全在庫の算出は「欠品頻度の発生確率」を統計的に推測するために「安全係数」を用います。この安全係数を使うためには、そもそも「使用量のばらつき」が平均を中心に左右対称の山型になるように分布する「正規分布」であることが前提です。「需要日が月末だけ」「特定のイベント前後だけ需要増」など極端に需要が偏った場合は正規分布の前提から離れるため、安全在庫の計算式を用いて適切な安全在庫量を算出することはできません。
安全在庫の最適化
安全在庫の設定は、ビジネス環境の変化に合わせて定期的に見直すことが重要です。例えば、季節要因による需要変動が大きい場合は、季節ごとに異なる安全在庫レベルを設定することが有効です。発注点を計算する際には、次のような要素を考慮すると良いでしょう:
- 需要パターンの変化: 成長トレンドや季節性を分析し、将来の需要を正確に予測する。
- サプライヤーの信頼性: 配送の正確さや遅延頻度を考慮して、リードタイムの変動幅を評価する。
- 商品の重要度: 欠品が事業に与える影響が大きい重要商品には、より高い安全在庫レベルを設定する。
- 在庫保持コスト: 商品の保管コスト、陳腐化リスク、資金コストなどを考慮する。
安全在庫の最適化をサポート!「スマートマットクラウド」
発注点と安全在庫の適切な管理は、理論的には明確でも、実務では常に正確な在庫数を把握することが最大の課題となります。特に多品種の商品を扱う企業では、日々の在庫カウントは膨大な労力を要し、人的ミスも発生しがちです。
こうした課題を解決するために、IoT技術を活用した「スマートマットクラウド」が注目を集めています。
スマートマットクラウドは、物理的なIoT重量センサとクラウド技術を組み合わせた在庫管理システムです。商品や資材の下に専用マット(IoT重量センサ)を敷くだけで、アイテムの重量変化をリアルタイムで検知し、自動的に在庫数を算出します。
- リアルタイム在庫監視:専用マット上の重量変化を検知し、在庫数を自動計算
- クラウドに即時反映:専用マットからデータが転送され、クラウド内で記録・管理
- 自動発注機能:設定した発注点に達すると、自動で発注処理を実行
- 在庫推移の可視化:グラフ表示により、在庫の適正化を促進
この革新的なシステムにより、従来の在庫管理における多くの課題が解決できます。人手による棚卸作業が不要になり、常に正確な在庫情報が得られるため、理想的な発注点と安全在庫の運用が可能になります。
さまざまな自動発注に対応
お客様の発注先に合わせた文面でメール・FAXの送信が可能です。
置く場所を選びません
スマートマットはサイズ展開豊富。ケーブルレスで、冷蔵庫・冷凍庫利用も可能。
API・CSVでのシステム連携実績も多数
自社システムや他社システムと連携を行い、より在庫管理効率UPを実現します。
安全在庫の最適化に貢献したスマートマットクラウド導入事例
スマートマットクラウドはさまざまな業種で活躍しています。特に医療業界では、クリティカルな状況を引き起こす欠品を回避するあまり、過剰在庫が常態化しやすいという問題があります。今回は実際の在庫変動から在庫の最適化を行った事例を紹介します。