1回あたり60時間かかっていた棚卸工数を約50%削減!“置くだけ”管理で欠品と過剰在庫を一挙に解消!
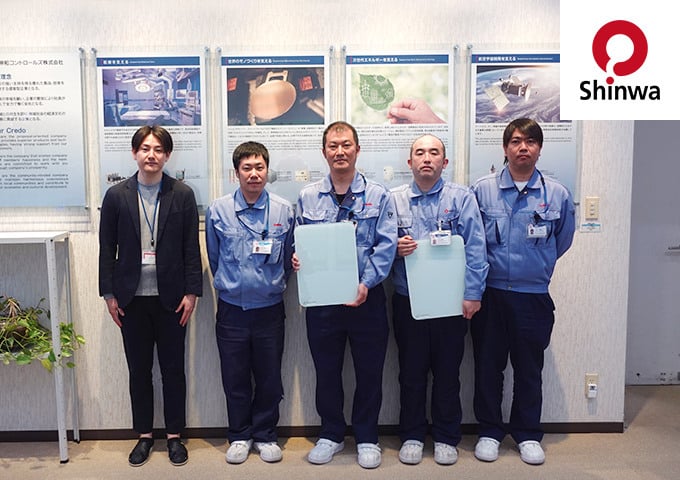
伸和コントロールズ株式会社
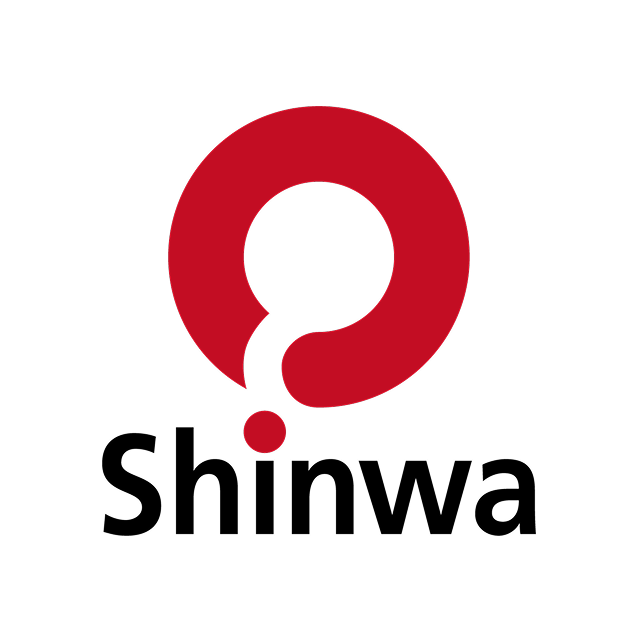
社名 | 伸和コントロールズ株式会社 |
業種 | 機械 |
課題 | 理論在庫と実在庫が食い違い、欠品と過剰在庫が同時に発生。棚卸の現場負担 |
効果 |
|
・手入力でのミス・漏れやカンバンの出し忘れなどで理論在庫と実在庫が食い違い、欠品と過剰在庫が同時に発生
・棚卸に1回あたり60時間以上かかり、現場への負担が大きかった
・欠品が起きると、現場だけでなく、購買部署やメーカーなどさまざまな場所で多大なロスを生んでいた
・手入力ミス削減と在庫データの精度が向上した
・リアルタイムで実在庫が把握できることで、棚卸時間や日々の入出庫作業工数が約50%削減
・スマートマットクラウドを含めたDXツール導入によるカイゼン活動の事例を、地域企業に共有し、地域全体の生産性や技術力の底上げに貢献できる
半導体、医療、航空宇宙、次世代エネルギーなど、様々な業界の最先端技術を支える伸和コントロールズ株式会社。今回は九州事業所の生産統括部 部長の石原さま、生産統括部 生産技術部1課 課長の古場さま、製造部 製造4課 課長の相川さま、製造部 製造3課 上級技師の中島さまにお話を伺いました。
御社の事業内容について教えてください
九州事業所では、主に半導体やフラットパネルディスプレイの製造プロセスで必要となる温度管理や湿度管理の装置を設計・製造・販売まで一括して行っています。
スマートマットクラウド導入前の在庫管理の課題を教えてください
人に頼った管理では入力ミスや入力忘れ、発注漏れが発生
実物を1個ずつ数える棚卸には1回あたり60時間以上かかることも
最も深刻だったのは、副資材(ネジやビス、チューブなど)の入出庫を人手で管理していた点です。現場作業者や副資材管理者など人に頼った管理ですね。
QRコードを読み込んで入庫数・出庫数を入力していたのですが、入力ミスや入力忘れが発生し、理論上の在庫と実際の在庫がしばしば食い違いました。
また、在庫が少なくなってきたら当然発注をかけないといけないため、「副資材購入カンバン」というものを使用して管理してました。そのカンバンを出せば、回収され発注してもらえるというシステムですが、それも入力間違いが起こり在庫数に違いが出ると、カンバンの出し忘れに繋がり、結果、発注漏れが頻繁に起きていたことも問題でした。
さらに、月1回と半年に1回ずつ実施している棚卸では、特に半期に1回の棚卸では1個ずつ実物を数えるため1回あたり60時間以上かかることもあり、現場への負担が大きかったことも課題でした。
ネジやビスなどの多種多様な副資材の入出庫管理を手作業で行っていたため、入力ミス・漏れから発注ミスが起きていた。棚卸には60時間以上かかることも
在庫データを見て発注するが、入力数を間違えていた場合、発注ミスが起こり、欠品に至るケースがあると生産面にも影響が出てしまいます。
現場で欠品が発生すると生産のコントロールが必要になり、その際、関連する購買部署やメーカーに短納期の対応を依頼することもあります。欠品が発生すると現場だけでなく、さまざまな場所で多大なロスをもたらしてしまいます。実際、このようなことが稀に起こっていました。
さらに、欠品は心理的にもプレッシャーになるため、逆に不安から発注しすぎて過剰在庫になることもありました。
欠品と過剰在庫が同時に起きているのが実情ですね。生産量が変動する中で「不安だから多めに手配」という行動が、結果的に在庫過多につながることもあります。
コロナ禍では入手困難な部品が多く、調達部門も含め社内全体が課題と感じていました。適正在庫をどう決めるか、Excelなどで試算しても時間がかかっていました。
スマートマットクラウドを知ったきっかけは何だったのでしょうか?
約2年前、展示会で在庫管理に使えるツールを探していた際にスマートマットクラウドと出会ったのがきっかけです。
昔から在庫管理と発注タイミングについての課題があったため、シンプルかつ現場で使いやすいスマートマットクラウドを拝見し、「これだ」と一目惚れのような形で導入を検討するようになりました。
スマートマットクラウドを選んだ際の決め手や、最も影響を与えた要因は何ですか?
自由度の高さと拡張機能の豊富さが魅力
大きく分けて2つあります。まず、スマートマットは、フラットな板であるため、いろいろな形状・サイズの副資材を置くだけで管理できる自由度の高さですね。
従来の箱型ソリューションだとサイズが合わない物は管理しづらかったのですが、スマートマットはそれを気にしなくて良い。
もう1つは、閾値設定による自動発注機能や、他システムとの連携機能など、重量を計測するだけにとどまらない拡張性です。
最初は「在庫数量が自動でわかれば充分」と思っていましたが、実際に話を伺う中で、「自動発注ができれば欠品や過剰在庫も防ぎやすい」といった付加価値を感じました。
スマートマットクラウドの導入により、どのような成果を期待していましたか?
手入力によるミスを削減し、棚卸時間も短縮
DXを進める大きな一歩に
スマートマットクラウドには色々な機能があるので、それらを生かして在庫金額の低減が期待できると考えておりました。
そのためには、入出庫時の手入力ミスを大きく減らすことです。作業者がネジを手に取る際、いちいち数をシステムに打ち込むのは煩わしく、ミスも起こりやすい。それを「置くだけ・取るだけ」で管理できれば確実に精度が上がります。
また、設定した発注点になったら、自動で発注できるという機能もありましたので、そちらでカンバンの出し忘れや在庫の出し忘れを防止できると考えました。
さらに、棚卸作業の時間短縮も狙いでした。今まで棚卸に毎回多大な人手と時間を費やしていましたが、リアルタイムで実在庫がわかるなら、1個ずつ実物を数える手間が減るはずだと。
それが実現すれば、現場作業や組み立てに集中しやすくなりますし、会社全体としてDXを進める大きな一歩になると考えました。
現在スマートマットクラウドでどういった物品を管理していますか?
主にネジ・ナット・ボルトなどの副資材が中心です。スマートマットは現状271台稼働していて、管理している部品点数は258点ほどになります。
まだ導入しきれていない資材も多いので、今後は残りの副資材、点数としては196点、スマートマット232台の導入を予定しています。事業所全体の副資材をほぼスマートマットクラウドに集約していく計画です。
最終的には「手入力管理をやめる」ことを目標に掲げていて、常に最新の在庫数がクラウド上で見られる状態を実現したい。その先には自動発注や、在庫コストの最適化といった追加ステップも見えています。
導入してどのような効果や改善が見られましたか?
入出庫工数と棚卸時間や約50%削減
5S向上の副次効果も
以前使っていましたQRコードでの入力という作業負担がなくなった分の効果が出ています。
まず、入出庫作業にかかる時間が目に見えて減りました。従来は15時間/週ほどかかっていた入力などの業務が、現在は7〜8時間/週と約半分まで作業時間が短縮できています。ミスも減り、作業者のストレスが軽くなったのは大きいですね。
次に、12月と6月に行っている年2回の実地棚卸の工数もほぼ半分になりました。ネジ関係の258点の棚卸に60時間/回ほどかかっていたのが、30時間/回程度で済むようになりました。クラウド上のデータをそのまま利用できるので、一個ずつ数える作業が不要になりました。
加えて、マット導入時に「どの棚に何を置くか」を再考した結果、倉庫内の整理整頓(5S)が進んだことも副次的な効果だと感じています。どこに何が置いてあるかわかりやすくなり、現場が混乱しにくくなりました。
作業現場から離れる時間が少なくなって、作業者からは「楽になった」という声が届いています。重量で自動管理してくれるので、人手による管理や入出庫作業をしなくてよくなったところが、作業者としては一番大きいです。
スマートマットクラウド導入後は「置くだけ・取るだけ」の入出庫管理になり、入出庫管理にかかる工数も約50%削減
スマートマットクラウドの活用について、今後の展望や期待することなどを教えてください
基幹システム連携でより効果的な運用を
閾値の見直しで、資材金額や欠品リスクの低減
現在は、ネジ・ナット・ボルトなどの副資材だけでの対応になっていますので、製造全体で管理できる対応を展開していきたいと思っています。
発注や在庫の従来のシステムやカンバンなどで対応している部分とスマートマットクラウドを併用して運用してますので、より効果的な運用を行って、目指してる効果を出していきたいと思います。
閾値を見直して、在庫低減にも繋げていきたいですし、動いていない在庫を把握し、資材数量の適正化、資材金額の低減、欠品リスクの削減にも力を入れていきたいですね。
現在は従来のカンバンとスマートマットクラウドを併用して運用中。将来的には購買部門とも連携し、発注まで自動化させる予定
今後広く社内展開していく計画や予定はありますか?あればその背景も教えてください
熊本・長野など他拠点へ展開
全社規模で在庫最適化
まずは熊本工場ですね。そこではまだ紙や手書きで在庫を管理する場面があり、データの正確性や工数の多さに課題を抱えています。九州事業所で確立した仕組みを横展開すれば同様の改善が期待できます。
また長野にも拠点がありますので、最終的には全社的にスマートマットを導入し、「どの工場に何がどれだけあるのか」をクラウド上で統合管理したいと考えています。
DX推進の流れでもあり、在庫に関わる情報を一元化できれば、コスト面・生産面ともに大きなメリットが出るだろうと思っています。
貴社では地域貢献を掲げていますが、積極的なDX推進も地域貢献に繋がっていますか?
社内のDXノウハウを地域に還元
企業連携でさらなる発展へ
生産効率が上がれば、品質が安定し、コスト削減にも繋がります。
その結果、受注が増えたり雇用が広がったりすることで、地域経済にプラスのインパクトを与えられると考えています。
また、スマートマットクラウドを含む、さまざまなカイゼン活動の事例発表も、今後地域の皆さまへ実施する予定です。
同じ悩みを抱える企業さんは多いと思うので、我々の成功事例を発信すれば、「どうやってDXを進めたのか」の実例として役立ててもらえるでしょう。
地域企業同士でノウハウを共有し合えば、地域全体の生産性や技術力が底上げされる可能性があります。そうした形で地域貢献を進めていきたいですね。
人による管理で発生するミスや漏れにより、理論在庫と実在庫が食い違い、欠品と過剰在庫が同時に発生するという課題を抱えていらした伸和コントロールズさま。在庫管理を見える化することで、副資材の管理効率化や棚卸時間の削減を実現しながら、さらなる社内展開や地域貢献に向けた取り組みを進めているとのお声、大変うれしい限りです。管理品数が多い企業さま、在庫管理・発注に課題を抱えている多くの企業さま、現場スタッフの皆さまのお役立ちができますよう、今後も努力してまいります。
伸和コントロールズ株式会社|スマートマットクラウド導入の概要
- 導入目的
手入力でのミス・漏れによる欠品と過剰在庫と棚卸の負担解消
- 設置場所
事業所内
- 管理商材
ネジ・ナット・ボルトなどの副資材など
- スマートマット導入の決め手
自由度の高さと拡張機能の豊富さ